Дипломная работа: Анализ и пути снижения себестоимости продукции (на примере ЗАО "Атлант")
РЕФЕРАТ
Объём пояснительной записки 88 стр., рис. 7, табл. 34, источников 23, приложений 4.
Тема: Себестоимость продукции: анализ и пути снижения (на примере ЗАО «Атлант»).
Ключевые слова: себестоимость продукции, элементы затрат, технико-экономические показатели, объём производства продукции, анализ состояния, целевое планирование, пооперационный метод.
Объект исследования: головное предприятие ЗАО «Атлант».
Цель работы: на основании информации о развитии предприятия в прошлом и данных о производственно-хозяйственной и сбытовой деятельности за последние три года произвести анализ и установить возможные направления снижения себестоимости продукции.
В процессе изучения объекта исследования проведен анализ себестоимости продукции, выручки, прибыли и рентабельности производства за последние годы.
На основе полученных в результате анализа данных в проектной части предложены мероприятия по повышению эффективности системы управления затратами и снижению себестоимости продукции за счёт совершенствования: организационной структуры; методологии учета затрат; методологии управления затратами;
Суммарный годовой экономический эффект от предлагаемых мероприятий составляет 3 723 313 тыс. р.
СОДЕРЖАНИЕ
1. СЕБЕСТОИМОСТЬ ПРОДУКЦИИ: СУЩНОСТЬ, СОДЕРЖАНИЕ, ПОКАЗАТЕЛИ.
1.1 Сущность и содержание себестоимости продукции
1.2 Методы учета и распределения затрат, включаемых в себестоимость продукции
1.3 Показатели и пути снижения себестоимости продукции
2. МЗХ ЗАО «АТЛАНТ»: ЕГО ХАРАКТЕРИСТИКА И АНАЛИЗ РАБОТЫ
2.1 Краткая характеристика предприятия
2.2 Организационная структура управления МЗХ ЗАО «Атлант»
2.3 Анализ основных технико-экономических показателей работы предприятия
2.4 Анализ себестоимости продукции
2.4.1 Анализ динамики изменения затрат на производство
2.4.2 Факторный анализ себестоимости продукции
3. ПУТИ СНИЖЕНИЯ СЕБЕСТОИМОСТИ ПРОДУКЦИИ НА МЗХ ЗАО «АТЛАНТ»
3.1 Организационно-экономические мероприятия по усовершенствованию процесса управления затратами
3.1.1 Совершенствование организационной структуры управления затратами.
3.1.2 Совершенствование методологии управления затратами
3.1.3 Совершенствование методологии учета затрат
3.2 Совершенствование процесса производства печатной платы
4. ВЛИЯНИЕ ЭКОЛОГИЧЕСКИХ И ПРОИЗВОДСТВЕННЫХ ФАКТОРОВ УСЛОВИЙ ТРУДА НА СЕБЕСТОИМОСТЬ ПРОДУКЦИИ МЗХ ЗАО «АТЛАНТ» И МЕРОПРИЯТИЯ ПО ИХ УЛУЧШЕНИЮ
4.1 Экологическая оценка предприятия
4.2 Пути улучшения экологических условий труда
4.3 Мероприятия по улучшению экологических условий труда
ЗАКЛЮЧЕНИЕ
СПИСОК ЛИТЕРАТУРЫ
ПРИЛОЖЕНИЕ Б
ПРИЛОЖЕНИЕ В
ПРИЛОЖЕНИЕ Г
ПЕРЕЧЕНЬ УСЛОВНЫХ ОБОЗНАЧЕНИЙ
ЗАО – закрытое акционерное общество;
МЗХ – минский завод холодильников;
ABC – activity based costing;
ТМЦ – товарно-материальная ценность;
ТЭП – технико-экономические показатели;
БП – «Бережливое производство»;
ПП – печатная плата;
МПП – многосторонняя печатная плата;
ДПП – двухсторонняя печатная плата;
ОПП – односторонняя печатная плата;
РЭ – радиоэлемент;
ФШ – фотошаблон.
ВВЕДЕНИЕ
Себестоимость - основа соизмерения расходов и доходов, это не только важнейший экономический показатель деятельности предприятия, но и фактор конкурентной борьбы в условиях рыночной экономики. В себестоимости как в обобщающем экономическом показателе находят свое отражение все стороны деятельности предприятия: степень технологического оснащения производства и освоения технологических процессов; уровень организации производства и труда; степень использования производственных мощностей; экономичность использования материальных и трудовых ресурсов и другие условия и факторы, характеризующие производственно-хозяйственную деятельность. Поэтому решение проблемы снижения себестоимости продукции непосредственно связано с повышением эффективности работы всего предприятия т.к. снижение затрат на производство продукции может повлечь за собой снижение цены изделия на ту же величину при остающейся неизменной величине прибыли, и, как следствие этого, увеличение спроса на данную продукцию.
Управление затратами – средство достижения предприятием высокого результата. Оно не сводится только к снижению затрат, но и распространяется на все элементы управления.
С социально-экономических позиций необходимость снижения себестоимости продукции для предприятия заключается в следующем:
– в увеличении прибыли, остающейся в распоряжении предприятия;
– в появлении большей возможности для материального стимулирования работников и решения многих социальных проблем коллектива предприятия;
– в появлении возможности не только в простом, но и расширенном воспроизводстве;
– в улучшении финансового состояния предприятия и снижении степени риска банкротства;
– в возможности снижения продажной цены на свою продукцию, что позволяет в значительной мере повысить конкурентоспособность продукции и увеличить объем продаж;
– для акционерных обществ это является хорошей предпосылкой для выплаты дивидендов и повышения их ставки.
В качестве объекта исследования было выбрано головное предприятие объединения ЗАО «Атлант». МЗХ ЗАО «Атлант» - ведущий производитель бытовой техники в Республике Беларусь и единственный производитель холодильной техники бытового назначения. Основная доля произведенной продукции идет на экспорт. В среде рыночной конкуренции эффективное управление затратами приобретает первостепенное значение, т.к. снижение себестоимости продукции позволяет увеличивать размер получаемой прибыли, либо снижать цену, приобретая тем самым дополнительные конкурентные преимущества. Именно поэтому представляет интерес проанализировать себестоимость производимой продукции для выявления резервов снижения данного показателя.
Предмет исследования – себестоимость производимой продукции и пути её снижения.
Цель исследования – на основании информации о развитии предприятия в прошлом и данных о производственно-хозяйственной и сбытовой деятельности за последние три года произвести анализ и установить возможные направления снижения себестоимости продукции.
Достижение поставленной цели реализуется посредством решения следующих задач:
– анализ теории по исследуемой проблеме;
– выявление основных причин, влияющих на изменение себестоимости продукции;
– анализ организационной структуры и данных о производственно-хозяйственной деятельности предприятия;
– формирование предложений по снижению себестоимости;
– обоснование эффективности предлагаемых мероприятий.
Основным методом исследования экономического состояния объекта является детерминированный ретроспективный факторный анализ.
Детерминированный анализ применяется для исследования функциональных взаимосвязей между факторными и результативными показателями.
Последующий (ретроспективный) анализ проводится после совершения хозяйственных актов. Он используется для контроля над выполнением плана, выявления неиспользованных резервов, объективной оценки результатов деятельности предприятий.
Факторный анализ направлен на выявление величины влияния факторов на прирост и уровень результативных показателей.
Исследование производится на основании плановых и отчетных документов; положений об отделах, должностных инструкций; данных статистической и бухгалтерской отчетности.
1 СЕБЕСТОИМОСТЬ ПРОДУКЦИИ: СУЩНОСТЬ, СОДЕРЖАНИЕ, ПОКАЗАТЕЛИ
1.1 Сущность и содержание себестоимости продукции
Себестоимость продукции, работ, услуг представляет собой один из важнейших обобщающих показателей деятельности организации, отражающий эффективность использования всей совокупности ресурсов, результатов инновационной деятельности в области техники, технологии, организации труда, производства и управления. Являясь основой ценообразования и конкурентоспособности продукции, себестоимость постоянно повышается в силу следующих причин: повышения цен на материальные ресурсы; заработной платы в связи с ростом минимальной базовой величины и тарифной ставки первого разряда; переоценки основных фондов и, в связи с этим, повышения амортизационных отчислений; переоценки оборотных средств в связи с инфляционными процессами и т.д.
Слово «себестоимость» является типично русским. Русско-английские словари дают два варианта перевода данного термина – 1) cost, и 2) cost price. Первый вариант «cost» переводится на русский как затраты, издержки, расходы и себестоимость. Второй вариант несет значение о том, что цена продукта соответствует затратам на его производство. Таким образом, себестоимость какого-либо объекта означает величину затрат предприятия на производство данного объекта. Из описанной выше сущности себестоимости вытекает традиционное определение данного понятия [23, стр. 103].
Себестоимость продукции, работ и услуг - стоимостная оценка используемых в процессе производства продукции (работ, услуг) природных ресурсов, сырья, материалов, топлива, энергии, основных средств, нематериальных активов, трудовых ресурсов и других затрат на ее производство и реализацию.
Себестоимость продукции включает затраты, разнородные по составу и экономическому назначению, что вызывает необходимость их классификации.
Существует достаточно много принципов классификации затрат: прямые и накладные, постоянные и переменные, на продукт и на период, управляемые и неуправляемые. В рамках данной работы наиболее важным является разделение расходов на прямые и накладные.
Прямые расходы (англ. - direct costs) — это расходы, которые можно прямо отождествить с объектом затрат, и само существование объекта затрат является непосредственной причиной возникновения прямых расходов. Чаще всего в качестве прямых расходов выделяют прямые материальные расходы и прямые расходы на оплату труда.
Накладные расходы (англ. - overhead costs) — это расходы, которые не связаны напрямую с объектами затрат. Этот вид расходов не является прямым следствием существования какого-либо объекта затрат. Причиной накладных расходов является либо группа объектов затрат, либо существование компании в целом. Обычно в качестве накладных расходов выделяют затраты на обслуживание и переналадку оборудования, административные расходы, коммерческие расходы.
Разделение расходов на прямые и накладные носит относительный характер и зависит от выбранного уровня объекта затрат. При смене данного уровня накладные расходы могут становиться прямыми, а прямые — накладными. Так, например, расходы на наладку оборудования перед запуском производства каждой партии будут прямыми для уровня партии и накладными для уровня единицы продукции. Расходы на рекламу какого-либо товара будут прямыми для уровня товара и накладными для уровней единицы и партии продукции. Состав затрат, включаемых в себестоимость продукции, определяется Основными положениями по составу затрат, включаемых в себестоимость продукции (работ, услуг). В общем случае в себестоимость продукции входят [5]:
– затраты, непосредственно связанные с производством продукции (работ, услуг);
– затраты, связанные с производством природного сырья;
– затраты на подготовку и освоение производства;
– затраты некапитального характера;
– затраты, связанные с изобретательством и рационализаторством;
– затраты на обслуживание производственного процесса;
– затраты по обеспечению нормальных условий труда и техники безопасности;
– текущие затраты, связанные с содержанием и эксплуатацией фондов природоохранного назначения;
– затраты, связанные с управлением производством;
– затраты, связанные с подготовкой и переподготовкой кадров;
– затраты, связанные с наймом рабочей силы;
– затраты по транспортировке работников к месту работы;
– дополнительные затраты, связанные с осуществлением работ вахтовым методом;
– обязательные отчисления от всех видов оплат труда работников по установленным законодательством нормам в фонд социальной защиты населения и фонд занятости;
– отчисления по обязательному медицинскому страхованию в соответствии с установленным законодательством порядком;
– платежи по страхованию имущества, грузов и риска непогашения кредитов;
– плата по процентам за ссуды;
– оплата услуг банков;
– отчисления в социальные отраслевые и межотраслевые внебюджетные фонды;
– затраты, связанные со сбытом продукции;
– затраты, связанные с содержанием помещений;
– затраты на воспроизводство основных производственных фондов;
– износ по нематериальным активам;
– начисления на заработную плату;
– другие виды затрат, включаемых в себестоимость продукции (работ, услуг) в соответствии с установленным законодательством порядком.
Не подлежат включению в себестоимость продукции (работ, услуг): затраты на выполнение самим предприятием или оплату им работ (услуг), не связанных с производством продукции; затраты на выполнение работ по строительству, оборудованию и содержанию культурно-бытовых и других объектов, находящихся на балансе предприятий.
Для учета и планирования затрат на производство и реализацию продукции применяются две взаимодополняющие классификации: поэлементная и калькуляционная (по статьям расходов).
Затраты, составляющие себестоимость продукции, могут группироваться в соответствии с их экономическим содержанием. В этом случае имеет место группировка затрат по элементам (поэлементная классификация затрат). Данная группировка затрат необходима в первую очередь для определения смет затрат, но позволяет определять задания по снижению себестоимости продукции и содержит следующие группы:
– материальные затраты (за вычетом возвратных отходов);
– расходы на оплату труда, учитываемые при ценообразовании и налогообложении (фонд оплаты труда);
– отчисления на социальные нужды, где отражаются обязательные отчисления по установленным законодательствам нормам в фонд социальной защиты населения, государственный фонд содействия занятости от всех видов оплаты труда работников не зависимо от источников выплат (кроме тех, на которые страховые взносы не начисляются).
– амортизация основных средств и нематериальных активов, которая отражает сумму амортизационных отчислений по основным средствам и нематериальным активам, исчисленную исходя из амортизируемой стоимости основных средств и нематериальных активов в установленном законодательством порядке;
– прочие расходы для отражения всех затрат, не вошедших в вышеперечисленные элементы.
В целях отражения места возникновения затрат на производство и реализацию продукции (работ, услуг), их учета и калькулирования, применяется группировка затрат по статьям (калькуляционная классификация). Типовая группировка затрат по статьям включает:
– сырье и материалы;
– возвратные отходы;
– покупные полуфабрикаты и услуги производственного характера сторонних предприятий и организаций;
– топливо и энергия на технологические цели;
– заработная плата основных производственных рабочих;
– отчисления на социальные нужды;
– износ спецоснастки и спецоборудования;
– общепроизводственные расходы;
– общехозяйственные расходы;
– потери от брака;
– прочие производственные расходы;
– коммерческие расходы.
Сумма одиннадцати первых статей образует производственную себестоимость продукции, а сумма двенадцати статей - полную себестоимость продукции.
1.2 Методы учета и распределения затрат, включаемых в себестоимость продукции
Понятие «себестоимость» само по себе не подразумевает метода, которым рассчитываются затраты для производства какого-либо объекта.
В зависимости от характера организации и технологии производства применяются различные способы определения себестоимости продукции. В промышленности применяются различные методы расчета себестоимости.
Метод расчета себестоимости объекта - отнесение или распределение части затрат предприятия на данный объект. Понятия «отнесение» и «распределение» в данном случае схожи и означают сопоставление затрат с конечным объектом косвенным методом. Однако последнее чаще применяется в случае большего количества объектов затрат и в отношении каждого конкретного объекта тоже является «отнесением». Далее рассмотрим различные методы распределения или отнесения затрат. Выделяют три основных метода распределения затрат [2, стр. 24]:
– прямое отслеживание;
– причинно-следственное распределение;
– условное распределение.
Прямое отслеживание затрат предполагает, что путем физического наблюдения затраты могут быть точно отнесены на конечный объект. Этот способ является наиболее точным и применяется чаще всего в отношении переменных издержек. Основной недостаток метода прямого отслеживания заключается в том, что может потребоваться слишком много ресурсов для физического наблюдения, чтобы отследить, куда идут затраты.
Метод распределения издержек путем установления причинно-следственных связей должен быть использован тогда, когда невозможно осуществить прямое отслеживание затрат, или когда это не эффективно с точки зрения затрат на ведение учета. Этот метод распределяет издержки исходя из долгосрочных причин. Данный метод также имеет свои недостатки. Он предполагает, что существует только одна причина, один фактор затрат. В результате применение метода будет не корректно для затрат, которые имеют два или более фактора.
Метод условного распределения используется, когда нельзя применить два вышеназванных метода. Он похож на причинно-следственный метод, за исключением того, что базис распределения издержек не является причиной издержек. В большинстве случаев, это какая-то уже отслеживаемая величина, например, объем продаж, объем продукции, затраты на труд основных рабочих. Так как база распределения издержек не является причиной, этот метод будет давать менее точные результаты, чем два вышеназванных метода. Возможно, распределение издержек будет и правильным – это произойдет в случае сильной корреляции базы распределения и причинного фактора. Но даже при правильном распределении издержек данный метод наименее применим для контроля над издержками. Сравнительный анализ трех способов отслеживания и распределения издержек по конечным объектам затрат приведен в таблице 1.1.
Таблица 1.1 - Методы распределения затрат
Метод | Средняя точность | Затраты на ведение учета | Применимость для контроля затрат |
Прямое отслеживание |
Высокая | Высокие, требуются значительные ресурсы |
Средняя, по причине отсутствия анализа факторов затрат |
Причинно-следственный | Высокая | Средние | Высокая |
Условное распределение |
Низкая | Низкие | Низкая |
Если издержки значимы для принятия решений, то оптимальным, с точки зрения соотношения выгод по использованию и затрат на получение информация, является способ отслеживания путем установления причинно-следственных связей. Преимущество данного метода – возможность аккумулировать издержки на различных этапах цепочки причинно-следственных связей. Каждый из методов отслеживания затрат нашел свое применение в определенной системе расчета себестоимости (таблица 1.2).
Прямой метод – в директ-костинг, прямой в сочетании с условным – в традиционной системе, прямой в сочетании с причинно-следственным – в функциональных системах (АВС системах).
Таблица 1.2 Методы расчета себестоимости
Методы | Директ-костинг | Традиционная система | Пооперационная система (АВС метод) | Позаказная система | Попроцессная |
Прямые |
Прямое отслеживание |
Прямое отслеживание |
Прямое отслеживание |
Прямое отслеживание |
Условное распределение |
Косвенные | Нет | Условное распределение | Причинно-следственные связи |
Прямое отслеживание |
Прямое отслеживание |
Директ-костинг подходит для производственных предприятий с низкой долей косвенных затрат.
Традиционная система – наиболее популярная система в отечественной практике.
Пооперационная система. Метод АВС позволяет предприятию с высокой степенью достоверности определять стоимость и производительность операций, оценивать эффективность использования ресурсов и вычислять себестоимость продукции (работ, услуг). Часто данные, полученные таким методом, радикально отличаются от результатов традиционных методов калькуляции.
Позаказная система учета затрат применяется в индивидуальном, мелкосерийном производствах сложных изделий. При данном методе объектом учета и калькулирования является отдельный производственный заказ, выдаваемый на заранее определенное количество продукции (изделий), объем работ, услуг.
Попроцессная система применяется в случаях, когда готовый продукт одного процесса становится полуфабрикатом для другого процесса. Усреднение затрат, принятое при попроцессном методе, приводит к неточностям в расчетах, в частности, когда продукт или составляющие его материальные компоненты не полностью однородны.
Таким образом систему распределения затрат следует выбирать исходя из типа предприятия, его структуры затрат и потребностей руководства в управленческой информации.
В связи с ростом косвенных затрат, не поддающихся учету и распределению прямым методом, встает вопрос о методах их распределения на объекты себестоимости. Выбор метода позволит определить возможности системы управленческого учета по подготовке значимой для управленческих решений информации, в частности, информации о себестоимости.
Наиболее популярной системой в отечественной практике является традиционная система учета затрат. Рассмотрим данную систему более детально.
Простые традиционные системы учета затрат распределяют косвенные издержки с использованием единой тарифной ставки накладных расходов для всей организации в целом. Более сложные традиционные системы выделяют на предприятии пулы затрат или центры издержек. Общие расходы, аккумулируемые в каждом центре издержек, затем распределяются по конечным объектам с использованием отдельной базы распределения для каждого такого центра. Такой подход является двухэтапным: на первом этапе затраты распределены по центрам, а на втором – по конечным объектам затрат. Количественная основа распределения затрат, которая используется при распределении затрат по конечным объектам, представляет собой базу распределения затрат.
Традиционные системы имеют, как правило, меньше баз распределения на этапе распределения по конечным объектам затрат, чем на этапе распределения по центрам. К базам распределения обычно относятся: часы труда основных работников, часы работы оборудования и число единиц выпущенной продукции. Другие базы используются редко. Таким образом, модель традиционных систем предполагает, что величина накладных расходов зависит главным образом от часов труда основных работников, часов работы оборудования и числе единиц выпущенной продукции. Однако существуют и другие базы распределения затрат, использование которых встречается в традиционных системах:
– основные производственные материалы;
– основные затраты.
Наиболее существенным недостатком традиционных систем расчета себестоимости является искажение себестоимости. Причина искажений заключается в том, что используемая база распределения затрат не соответствует реальным причинно-следственным связям между затратами и конечными объектами. Наиболее часто используемые базы распределения:
– количество единиц продукции;
– количество часов труда основных рабочих (стоимость труда основных рабочих);
– количество часов работы оборудования;
– стоимость основных материалов;
– основные затраты.
Искажения происходят по определенным причинам и чаще всего ими являются характеристики продуктов. К числу основных из них относятся:
– сложность продуктов при сборке, количество комплектующих или видов материалов;
– стоимость материалов;
– размеры партии и заказов;
– объемы выпуска продуктов.
Искажение себестоимости продуктов, которые различаются по сложности сборки и количеству комплектующих и видов материалов, происходит по причине приравнивания себестоимости более сложных продуктов к себестоимости менее сложных, хотя первые потребляют большее количество ресурсов предприятия. Таким образом, себестоимость более сложных продуктов занижается, а менее сложных – завышается. Если система расчета использует в качестве базы распределения труд основных рабочих или время работы оборудования – то нельзя сделать прямого вывода относительно искажений различающихся по сложности сборки продуктах. Однако при использовании этой базы все равно искажается себестоимость продуктов, различающихся по количеству комплектующих и видов материалов по вышеназванным причинам. Аналогичная ситуация происходит и при использовании в качестве базы распределения стоимости материалов или стоимости основных затрат. В этом случае считается, что и сложные и простые продукты имеют одинаковое соотношение затрат на материалы к остальным затратам, в частности к косвенным.
Теперь рассмотрим искажения себестоимости продуктов, отличающихся по стоимости материалов. Явные искажения себестоимости проявятся, если традиционная система будет использовать в качестве базы распределения затрат стоимость материалов или величину основных затрат. Тогда расчет осуществляется исходя из предположения, что косвенные затраты содержатся в каждом продукте пропорционально затратам на материалы или на материалы плюс труд. Однако, недорогие в отношении материалов продукты могут требовать больших затрат при разработке или проверке качества. Получается, что продукты с большей стоимостью материалов притягивают на себя еще большее количество косвенных затрат и их себестоимость завышается.
Искажение себестоимости продуктов, отличающихся по размеру партии при изготовлении или величины заказа, происходит следующим образом. Очевидно, что производство партии или изготовление заказа требует определенных, и зачастую значительных, затрат на наладку оборудования, закупку партии комплектующих, возможно, определенные инженерные работы. В реальности продукты в более мелких партиях при прочих равных всегда дороже аналогичных продуктов в крупных партиях, потому, что несут больший груз общих по отношению к производимой партии издержек. При использовании любой из распространенных баз распределения в традиционной системе (количество единиц продукции, труд основных рабочих, часы оборудования, стоимость материалов, основные затраты) – продукция мелких и крупных партий будет стоить одинаково. Таким образом, себестоимость продукции в мелких партиях занижается, а себестоимость продукции в крупных партиях завышается.
Искажения себестоимости, связанные с объемом производимой продукции, проявляются по причине того, что каждый продукт требует затрат по разработке, закупкам сырья, проверке качества и других сопутствующих внутрифирменных услуг, и эти затраты находятся в минимальной зависимости от объема продукции. Продукты с большим объемом выпуска при условном распределении склонны перетягивать на себя большее количество косвенных расходов, а продукты с меньшими объемами – меньшее. Таким образом, себестоимость продуктов с большим объемами производства в традиционных системах завышается, а с небольшими – занижается.
Обобщим наличие искажений себестоимости при различных комбинациях характеристик продуктов и баз распределения в таблице 1.3:
Таблица 1.3 Сводная таблица искажений себестоимости
Фактор | Характеристика товара | Количество единиц продукции | Труд основных рабочих | Часы работы оборудования | Стоимость материалов | Основные затраты |
Сложность продуктов | Сложный продукт | Занижение | Занижение | Занижение | Занижение | Занижение |
Стоимость материалов | Нематериалоемкий | Нет однозначных искажений | Нет однозначных искажений | Нет однозначных искажений | Занижение | Занижение |
Размер партии | Продукт в небольшой партии | Занижение | Занижение | Занижение | Занижение | Занижение |
Объем выпуска |
Продукт с низким объемом производства | Занижение | Занижение | Занижение | Занижение | Занижение |
Как видим, условное распределение затрат, используемое в традиционных системах, не может позволить точным образом рассчитать себестоимость на предприятии с большим числом бизнес-процессов. Условное распределение в традиционных системах предполагает, что косвенные затраты (в частности затраты на маркетинг, разработку и тестирование продуктов, контроль качества и другое) содержатся в себестоимости продукции в той же пропорции, что и труд основных рабочих или затраты на материалы. Очевидно, что для различных продуктов, производимых на одном предприятии, соотношение косвенных затрат с прямыми основными в структуре себестоимости может быть разным. Чем больше величина таких различий в структуре себестоимости продукции на предприятии – тем сильнее искажается себестоимость данной продукции при расчете ее традиционным методом.
Рассмотрим возможные последствия применения менеджментом неверной информации о себестоимости:
Во-первых, это неправильное установление продажных цен на продукцию предприятия. Установление меньшей цены вследствие заниженной себестоимости уменьшит потенциальную прибыль от производства и реализации данного продукта или, в крайнем случае, вообще приведет к убыточному производству. Установление завышенных цен на продукт с реально более низкой себестоимостью может привести к потере доли рынка и объемов продаж.
Во-вторых, возможно принятие решения о прекращении производства прибыльной продукции, основываясь на информации о завышенной себестоимости и соответственно, отрицательной рентабельности.
В-третьих, возможно производство неприбыльных продуктов и занятие неприбыльными видами деятельности.
Таким образом, использование традиционных систем расчета себестоимости может привести к искажениям информации о затратах на производство продукции, а значит к ошибкам при принятии управленческих решений. Интенсивная глобальная конкуренция сделала ошибки в результате неправильных решений на основе недостаточной информации более вероятными и дорогостоящими. За последние годы возросла альтернативная стоимость плохой системы информации, и снизились расходы на ведение более современных систем учета затрат, а также вырос спрос на более точные данные по себестоимости продукции. Все это стало фоном, на котором появилась потребность в более эффективных инструментах расчета и управления себестоимостью.
1.3 Показатели и пути снижения себестоимости продукции
В общем виде все основные показатели себестоимости можно представить в виде следующих группировок (таблица 1.4).
Таблица 1.4 Классификация показателей себестоимости продукции
Классификационный признак | Показатель |
По охвату затрат |
цеховая себестоимость |
фабрично-заводская (производственная) себестоимость |
|
полная себестоимость | |
По длительности периода |
среднемесячная себестоимость |
среднеквартальная себестоимость |
|
среднегодовая себестоимость | |
По методу расчета |
плановая себестоимость |
нормативная себестоимость |
|
сметная себестоимость |
|
фактическая себестоимость | |
По объектам подсчета |
себестоимость сравнимой продукции |
себестоимость несравнимой продукции |
|
себестоимость всей товарной продукции |
|
себестоимость единицы изделия |
Более подробно остановимся на отдельных показателях себестоимости в зависимости от объекта подсчета, т.к. данные показатели будут использованы в последующем анализе. В зависимости от анализируемого объекта (единица продукции, объем производства подразделения или организации в целом) различают следующие показатели себестоимости [3, стр. 104]:
а) Затраты на рубль объема произведенной продукции.
Для характеристики динамики себестоимости всей (сравнимой и несравнимой) продукции используется показатель «затраты на рубль товарной продукции», исчисляемый путем деления себестоимости производимой товарной продукции в каждом году на ее объем в стоимостном выражении. В этом показателе затраты на производство приводятся к одной базе, что дает возможность анализировать данные об относительных уровнях себестоимости за несколько лет подряд:
, (1)
где z – себестоимость каждого вида выпускаемой продукции, работ, услуг;
q – количество единиц продукции каждого вида;
p – цена единицы продукции.
а) Полная себестоимость объема произведенной продукции.
Себестоимость продукции определяется как сумма всех затрат, приходящихся на изготовление данного объема и ассортимента продукции, работ, услуг.
б) Себестоимость единицы продукции.
Данный показатель представляет собой абсолютную сумму затрат по калькуляционным статьям расходов на производство единицы соответствующего вида продукции или услуг в планируемом периоде. Если номенклатура выпускаемой продукции велика, то плановые калькуляции могут составляться по группам однородных изделий и отдельным типовым представителям этих групп. Себестоимость единицы изделий, производимых впервые, определяется на основе сметных калькуляций. При определении себестоимости единицы изделия необходимо соответствие ее натуральному измерителю, принятому для данного изделия в прейскурантах.
Возможности снижения себестоимости продукции можно выявить и анализировать по двум направлениям - по источникам и факторам.
Под источниками понимаются затраты, за счет экономии которых снижается себестоимость продукции. К ним относятся затраты живого и овеществленного труда, административно-управленческие расходы.
Выделяют следующие источники, по которым можно наметить резервы снижения себестоимости:
– снижение затрат на оплату труда;
– снижение материалоемкости продукции;
– сокращение затрат на управление и обслуживание производства;
– экономия внепроизводственных потерь и расходов;
– ликвидация непроизводительных потерь и расходов.
Под факторами понимают мероприятия, вызывающие изменения себестоимости продукции. Все факторы подразделяются на народнохозяйственные, внутриотраслевые и внутрипроизводственные. Народнохозяйственные факторы - это изменение цен на материалы, конструкции, тарифов на электроэнергию, тарифных ставок. Внутриотраслевые факторы предусматривают улучшение материально-технического снабжения, повышения уровня концентрации производства и укрупнения предприятий, специализацию, совершенствование структуры управления, развитие кооперирования. Внутрипроизводственные факторы предусматривают внедрение укрупненных сборных конструкций и деталей, экономию материальных ресурсов, увеличение объема выполняемых работ, улучшение использования машин, механизмов, оборудования.
Классификация источников и факторов снижения себестоимости представлена в таблице 1.5 [23, стр. 108].
Таблица 1.5 Источники и факторы снижения себестоимости
Источники | Факторы |
Снижение затрат на оплату труда | Применение трудосберегающих технологий, улучшение организации производства |
Снижение материалоемкости продукции | Рациональное и экономное применение материальных ресурсов, применение ресурсосберегающих технологий |
Сокращение затрат на управление и обслуживание производства | Изменение объема и структуры продукции |
Экономия внепроизводственных потерь и расходов | Повышение качества продукции |
Ликвидация непроизводительных потерь и расходов | Совершенствование стимулирования |
Одним из вариантов снижения себестоимости продукции является применение трудосберегающих технологий и улучшение организации производства, что ведет к повышению производительности труда. С ростом производительности труда сокращаются затраты труда в расчете на единицу продукции, а следовательно, уменьшается и удельный вес заработной платы в структуре себестоимости. Увеличение выработки продукции на одного рабочего может быть достигнуто за счет осуществления организационно-технических мероприятий, благодаря чему изменяются, как правило, нормы выработки и соответственно им расценки за выполняемые работы. Увеличение выработки может произойти и за счет перевыполнения установленных норм выработки без проведения организационно-технических мероприятий. Нормы выработки и расценки в этих условиях, как правило, не изменяются.
В первом случае, когда изменяются нормы выработки и расценки, предприятие получает экономию на заработной плате рабочих. Объясняется это тем, что в связи со снижением расценок доля заработной платы в себестоимости единицы продукции уменьшается. Однако это не приводит к снижению средней заработной платы рабочих, так как приводимые организационно-технические мероприятия дают возможность рабочим с теми же затратами труда выработать больше продукции. Таким образом, проведение организационно-технических мероприятий с соответствующим пересмотром норм выработки позволяет снижать себестоимость продукции за счет уменьшения доли заработной платы в единице продукции одновременно с ростом средней заработной платы рабочих.
Во втором случае, когда установленные нормы выработки и расценки не изменяются, величина затрат на заработную плату рабочих в себестоимости единицы продукции не уменьшается. Но с ростом производительности труда увеличивается объем производства, что приводит к экономии по другим статьям расходов, в частности сокращаются расходы по обслуживанию производства и управлению. Происходит это потому, что в общепроизводственных расходах значительная часть затрат (а в общехозяйственных почти полностью) - условно-постоянные расходы (амортизация оборудования, содержание зданий, содержание цехового и общезаводского аппарата и другие расходы), не зависящие от степени выполнения плана производства. Это значит, что их общая сумма не изменяется или почти не изменяется в зависимости от выполнения плана производства. Отсюда следует, что, чем больше выпуск продукции, тем меньше доля цеховых и общезаводских расходов в ее себестоимости.
Важнейшее значение в борьбе за снижение себестоимости продукции имеет соблюдение строжайшего режима экономии на всех участках производственно-хозяйственной деятельности предприятия. Последовательное осуществление на предприятиях режима экономии проявляется прежде всего в уменьшении затрат материальных ресурсов на единицу продукции, сокращении расходов по обслуживанию производства и управлению, в ликвидации потерь от брака и других непроизводительных расходов.
Учитывая удельный вес материальных затрат в структуре себестоимости продукции, даже незначительное сбережение сырья, материалов, топлива и энергии при производстве каждой единицы продукции в целом по предприятию дает крупный эффект.
Предприятие имеет возможность влиять на величину затрат материальных ресурсов, начиная с их заготовки. Сырье и материалы входят в себестоимость по цене их приобретения с учетом расходов на перевозку, поэтому правильный выбор поставщиков материалов влияет на себестоимость продукции. Важно обеспечить поступление материалов от таких поставщиков, которые находятся на небольшом расстоянии от предприятия, а также перевозить грузы наиболее дешевым видом транспорта. При заключении договоров на поставку материальных ресурсов необходимо заказывать такие материалы, которые по своим размерам и качеству точно соответствуют плановой спецификации на материалы, стремиться использовать более дешевые материалы, не снижая в то же время качества продукции. Условием снижения затрат сырья и материалов на производство единицы продукции является также улучшение конструкций изделий и совершенствование технологии производства, использование прогрессивных видов материалов, внедрение технически обоснованных норм расходов материальных ценностей.
Сокращение затрат на обслуживание производства и управление снижает себестоимость продукции. Размер этих затрат на единицу продукции зависит не только от объема выпуска продукции, но и от их абсолютной суммы. Чем меньше сумма общепроизводственных и общехозяйственных расходов в целом по предприятию, тем при прочих равных условиях ниже себестоимость каждого изделия.
Резервы сокращения цеховых и общезаводских расходов заключаются, так же, в упрощении и удешевлении аппарата управления, в экономии на управленческих расходах. В состав общепроизводственных и общехозяйственных расходов в значительной степени включается также заработная плата вспомогательных и подсобных рабочих. Проведение мероприятий по механизации вспомогательных и подсобных работ приводит к сокращению численности рабочих, занятых на этих работах, а следовательно, и к экономии цеховых и общезаводских расходов. Важнейшее значение при этом имеют автоматизация и механизация производственных процессов, сокращение удельного веса затрат ручного труда в производстве. Автоматизация и механизация производственных процессов дают возможность сократить и численность вспомогательных и подсобных рабочих в промышленном производстве. Сокращению цеховых и общезаводских расходов способствует также экономное расходование вспомогательных материалов, используемых при эксплуатации оборудования и на другие хозяйственные нужды.
Значительные резервы снижения себестоимости заключены в сокращении потерь от брака и других непроизводительных расходов.
2 МЗХ ЗАО «АТЛАНТ»: ЕГО ХАРАКТЕРИСТИКА И АНАЛИЗ РАБОТЫ
2.1 Краткая характеристика предприятия
Начало существования завода, как отдельного предприятия, положено Решением Исполнительного комитета Минского городского Совета депутатов трудящихся 18 декабря 1958 года № 1258 «Об образовании завода газовой аппаратуры». 24 августа 1959 года Совет Министров БССР издал Постановление «Об организации производства бытовых холодильников на Минском заводе газовой аппаратуры». В этом же году была разработана производственная программа по выпуску 50 тыс. холодильников в год.
Основной продукцией, выпускаемой МЗХ ЗАО «Атлант», являются холодильники и морозильники.
На Минском заводе холодильников в настоящее время выпускаются бытовые холодильники и морозильники, разные по объему (от 30 до 400 л), функциональным возможностям (однокамерные и двухкамерные, с верхним и нижним расположением морозильной камеры, с одним и двумя компрессорами, с электронным блоком управления и индикации). Особенностями вновь разработанных и запущенных в серию моделей холодильников являются применение двух компрессоров, использование системы озонобезопасной заливки двери и шкафа, новый наружный и внутренний дизайн, изготовление деталей из металлопласта и прозрачного полистирола.
При разработке новых моделей бытовых холодильников и морозильников «Атлант» совершенствуются конструкции изделий, улучшается их энергоэффективность.
Минский завод холодильников поставляет свою продукцию в Австралию, Германию, Йемен, Латвию, Литву, Монголию, Словакию, Францию, Швецию, Эстонию (всего в 34 страны мира). Ассортимент холодильников и морозильников в настоящее время представлен 35 моделями, большинство из которых могут иметь различное исполнение.
В последнее время Минский завод холодильников стал известен как производитель промышленного оборудования. Завод имеет успешный опыт в создании автоматизированных и механизированных транспортно-складских, сборочных систем, которые можно использовать для любого производства. В короткие сроки согласно требованиям заказчика на предприятии изготавливаются воздуховоды и комплектующие для систем вентиляции высокого качества.
Использование прогрессивных технологий в проектировании и изготовлении специального технологического оборудования также позволяет Минскому заводу холодильников успешно выполнять заказы других предприятий. Инструментальное производство завода предлагает проектирование литьевых форм, вакуумформ, штампов, приспособлений; изготовление и внедрение технологической оснастки; обучение специалистов обслуживания оснастки.
В целом, рынок сбыта продукции сформировался на базе стран бывшего СССР и, соответственно, действовавшей системы распределения. На сегодняшний день поставку продукции МЗХ ЗАО «Атлант» по странам и долю на основных рынках можно распределить следующим образом (таблица 2.1, таблица 2.2).
Таблица 2.1 Основные потребители продукции МЗХ ЗАО «Атлант»
Наименование страны-потребителя | Доля в общей структуре потребления продукции, % |
Республика Беларусь | 18,4 |
Россия | 60,2 |
Украина и Молдова | 12 |
Дальнее зарубежье | 6,1 |
Страны Средней Азии и Закавказья | 3,3 |
ИТОГО | 100,0 |
Таким образом, из таблицы 2.1 видно, что основным потребителем продукции МЗХ ЗАО «Атлант» выступает Россия. На данный рынок поставляется более 60% всей произведенной продукции.
Таблица 2.2 - Доля МЗХ ЗАО «Атлант» на рынках бытовой техники
Наименование страны-потребителя | Доля в общей структуре потребления продукции, % |
Республика Беларусь | 88 |
Россия | 17 |
Украина и Молдова | 35 |
Дальнее зарубежье | 7 |
Страны Средней Азии и Закавказья | 30 |
Таблица 2.2 иллюстрирует, что из 100 единиц бытовой техники, в Республике Беларусь 88 единиц является техникой производства МЗХ ЗАО «Атлант», в Украине и Молдове – 35, в странах Средней Азии и Закавказья – 30. В тоже время рынок бытовой техники России, при 60% поставках произведенной продукции, занят бытовой техникой «Атлант» на 17%, что говорит о значительных объемах данного рынка и наличии перспектив его дальнейшего освоения.
Производственная структура предприятия состоит из цехов основного производства и цехов подготовки и обслуживания производства.
На предприятии имеются следующие основные цеха:
– прессово-сварочный цех;
– цех пластмасс;
– цех подсборки и теплоизоляции;
– механосборочный цех.
Вспомогательными цехами, занимающимися подготовкой и обслуживанием основного производства, являются:
– ремонтно-механический цех,
– энергосиловой цех;
– транспортный цех;
– ремонтно-строительный цех;
– опытно-экспериментальный цех;
– цех специального технологического оснащения.
Начинается технологический процесс в прессово-сварочном цеху. В нем производят основные металлические полуфабрикаты для холодильников, путем шлифовки и нарезки на определенную длину. Далее эти детали поступают на покраску и покрытие пленкой. В цехе пластмасс изготавливают необходимые пластмассовые детали (полки, панели двери, внутренние шкафы, уплотнители и др.) С помощью конвейеров металлические детали поступают в прессово-сварочный цех, в котором им предают необходимые формы для шкафа и двери. Далее детали поступают в цех подборки, где из комплектующих собирают различные модели холодильников и морозильников. В заключительном механосборочном цехе происходят конечные стадии изготовления продукции, приемо-сдаточные испытания и упаковка изделий. После чего холодильники поступают на склад.
2.2 Организационная структура управления МЗХ ЗАО «Атлант»
Минский завод холодильников является головным предприятием ЗАО «Атлант», что обуславливает единство системы управления. Организационную структуру ЗАО «Атлант» можно характеризовать как линейно-функциональную. Высший уровень управления представлен собранием Акционеров, правлением ЗАО и генеральным директором (президентом) ЗАО.
Высшим органом управления ЗАО «Атлант» является собрание Акционеров. К компетенции собрания относится изменение и дополнение устава общества; изменение уставного фонда общества; определение организационной структуры общества; избрание и отзыв членов выборных органов общества; определение основных направлений деятельности общества и др.
Руководство деятельностью ЗАО «Атлант» в период между собраниями акционеров осуществляется правлением, которое избирается из числа акционеров. Количественный состав правления формируется следующим образом: Государственный комитет по имуществу – три человека; Минское городское управление госимуществом и приватизации – один человек; Национальный банк Республики Беларусь – один человек; Минский завод холодильников – пять человек; Барановичский станкостроительный завод – три человека.
Исполнительное управление осуществляют президент ЗАО «Атлант» Шумило В.С., который одновременно является директором Минского завода холодильников и вице-президент ЗАО «Атлант» Решетко В.В., который одновременно является директором Барановичского станкостроительного завода.
Контроль финансово-хозяйственной деятельности ЗАО «Атлант», его структурных единиц, предприятий, филиалов и представительств, контроль над работой президента и вице-президента ЗАО осуществляется ревизионной комиссией ЗАО «Атлант», которая избирается сроком на три года в количестве девяти человек и действует на основании положения «О ревизионной комиссии акционерного общества».
В приложении А приведена организационная структура Минского завода холодильников ЗАО «Атлант». Как видно, генеральному директору подчиняются главный инженер и семь заместителей директора по функциям. Также в непосредственном подчинении генерального директора находится ряд подразделений, осуществляющих специфические функции: юридический отдел, отдел информационных технологий, служба безопасности и охраны и др.
Система оперативного управления представлена восемью службами:
– техническая служба, в функции которой входит модернизация и анализ надежности работы оборудования, организация технадзора, обеспечение предприятия всеми видами энергоресурсов, разработка и внедрение ноу-хау в технологии, внедрение оснастки, разработка и создание новых материалов, разработка конструкции и дизайна холодильников и т.д.;
– экономическая служба, которая определяет порядок ценообразования на продукцию, контролирует и согласовывает цены на ТМЦ, разрабатывает прогнозы социально-экономического развития на год, штатное расписание предприятия, начисляет работникам заработную плату и премии, разрабатывает график работы предприятия, занимается вопросами, связанными с обязательствами Общества, учетом имущества, хозяйственных операций, ТМЦ и денежных средств и др.;
– производственная служба, в ведении которой сосредоточены все вопросы основного производства: управление цехами основного производства МЗХ разработка годовых, квартальных и месячных планов производства продукции и т.д.;
– служба управления качеством осуществляет организацию и контроль над выполнением мероприятий по качеству, контроль надежности техпроцессов, анализ дефектов и отклонений, рационализацию, обеспечение послепродажного и сервисного обслуживания;
– коммерческая служба курирует вопросы о заключении договоров на поставку продукции, осуществляет анализ данных об отказах от продукции, количестве поставляемой продукции по номенклатуре, разрабатывает прогнозы развития спроса на продукцию на внутреннем и внешнем рынках и др.;
– служба снабжения и перевозок, которая занимается определением потребности в материально-технических ресурсах, подготавливает и заключает договора на поставку ресурсов, осуществляет распределение материально-технических ресурсов между подразделениями предприятия, следит за их рациональным использованием, выполняет все транспортные услуги предприятия;
– служба капитального строительства занимается планированием капитальных работ, обеспечением источников их финансирования и контролем работ, проводимых ремонтно-строительным цехом;
– служба персонала и социального развития осуществляет подбор, расстановку и воспитание кадров, разрабатывает планы подготовки и повышения квалификации рабочих, специалистов, служащих, руководителей, занимается социальными сторонами жизни предприятия: обеспечением жильем в общежитии и предоставлением услуг детских дошкольных учреждений и др.
Работу по контролю и учету затрат на производство осуществляет «Отдел планирования и экономического анализа», поэтому необходимо подробно рассмотреть выполняемые функции и структуру данного подразделения. Основные функции отдела [7]:
– осуществлять планирование и прогнозирование ТЭП по МЗХ в целом и в разрезе структурных подразделений. Разрабатывать и составлять годовые, квартальные и месячные планы и доводить до структурных подразделений МЗХ.
– анализировать выполнение ТЭП, контролировать соблюдение бюджетов доходов и расходов внутризаводскими подразделениями.
– планировать технико-экономические показатели и нормативы внутризаводским подразделениям на квартал с разбивкой по месяцам.
– осуществлять разработку документооборота для внутриэкономического планирования, учета и внедрения механизированной обработки информации в информационной системе предприятия.
– анализировать затраты, сметы накладных расходов представляемых предприятиями – смежниками для определения и согласования цен на детали, узлы изготовляемые для предприятия.
– разрабатывать и согласовывать цены на продукцию, работу, услуги оказываемую внутризаводским подразделениям и сторонним организациям.
– проводить расчет материальных затрат, определять плановую себестоимость продукции, работ и услуг, анализировать произведенные расчеты и корректировку их при необходимости. Планировать сметы накладных расходов, рассчитывать сметы по использованию прибыли на развитие и потребление.
– осуществлять анализ изменения цен на ТМЦ и их влияние на материальные затраты. Отслеживать динамику изменения и влияния цен. Требовать экономическое обоснование при пересмотре цен на ТМЦ. Вносить предложения о допустимом уровне роста цен на ТМЦ.
– формировать справочник цен на готовую продукцию, ТМЦ и вносить изменения, поправки, своевременно обеспечивать информацией пользователей.
– рассчитывать экономическую эффективность от внедрения мероприятий по снижению затрат в себестоимости и рационализаторских предложений.
– вести делопроизводство, организовывать систематизацию и хранение в соответствии с установленными сроками нормативно–справочных документов.
– контролировать экономическую деятельность структурных подразделений предприятия, соответствие цен на производимую продукцию, приобретаемые ТМЦ для обеспечения жизнедеятельности предприятия.
Организационная структура отдела представлена в приложении Б.
Анализируя организационную структуру МЗХ ЗАО «Атлант» в целом можно сделать вывод, что она имеет линейно-функциональную структуру и сформирована таким образом, чтобы максимально упростить и упорядочить систему производства, подчиненность персонала, передачу информации внутри завода.
Однако, что касается вопроса управления затратами и себестоимостью продукции в частности, на предприятии отсутствует аналитическая служба, отвечающая за комплексный анализ всех понесенных предприятием затрат в ходе производственно-хозяйственной деятельности.
2.3 Анализ основных технико-экономических показателей работы предприятия
Анализ экономического состояния предприятия проводится на основании технико-экономических показателей.
Перечень основных технико-экономических показателей представлен в таблице 2.3.
Таблица 2.3 – Основные технико–экономические показатели работы предприятия
Наименование показателей | Единица измерения | Период | Динамика | |||||
2006/07 | 2007/08 | |||||||
2006 | 2007 | 2008 | Абс. откл. | Относ. откл. | Абс. откл. | Относ. откл. | ||
1 | 2 | 3 | 4 | 5 | 6 | 7 | 8 | 9 |
Объем производства продукции | ||||||||
- в натуральном выражении | шт. | 897 340 | 965 294 | 1 006 509 | 67 954 | 1,08 | 41 215 | 1,04 |
- в сопоставимых ценах | млн.р. | 409 999 | 668 896 | 716 733 | 258 897 | 1,63 | 47 837 | 1,07 |
- в фактических ценах отчетного года | млн.р. | 486 827 | 635 766 | 682 800 | 148 939 | 1,31 | 47 034 | 1,07 |
Объем реализации продукции | ||||||||
- в натуральном выражении | шт. | 918 038 | 965 572 | 1 006 730 | 47 534 | 1,05 | 41 158 | 1,04 |
- в сопоставимых ценах | млн.р. | 419 456 | 669 089 | 716 890 | 249 633 | 1,60 | 47 802 | 1,07 |
- в фактических ценах отчетного года | млн.р. | 498 056 | 635 949 | 682 950 | 137 893 | 1,28 | 47 001 | 1,07 |
Выручка от реализации продукции, товаров, работ, услуг | млн.р. | 659 566 | 838 005 | 819 203 | 178 439 | 1,27 | -18 802 | 0,98 |
Себестоимость реализованной продукции, товаров, работ, услуг | млн.р. | 411 976 | 528 545 | 605 497 | 116 569 | 1,28 | 76 952 | 1,15 |
Прибыль от реализации продукции, товаров, работ, услуг | млн.р. | 128 106 | 169 465 | 126 634 | 41 359 | 1,32 | -42 831 | 0,75 |
Чистая прибыль | млн.р. | 81 631 | 123 561 | 83 103 | 41 930 | 1,51 | -40 458 | 0,67 |
Нераспределенная прибыль | млн.р. | 28 084 | 53 479 | 29 556 | 25 395 | 1,90 | -23 923 | 0,55 |
Рентабельность реализованной продукции | % | 31,10 | 33,10 | 20,90 | 0,60 | 1,03 | -7,60 | 0,69 |
Рентабельность продукции | % | 23,70 | 24,30 | 16,70 | 2,00 | 1,06 | -12,20 | 0,63 |
Рентабельность капитала | % | 22,00 | 28,80 | 16,30 | -1,20 | 0,95 | -4,50 | 0,78 |
Среднесписочная численность ППП | чел. | 15 086 | 15 114 | 15 108 | 28 | 1,00 | -6 | 1,00 |
Производительность труда ППП | млн.р./ чел. | 32,27 | 42,06 | 45,19 | 9,79 | 1,30 | 3,13 | 1,07 |
Средняя заработная плата за последний месяц периода | тыс. р. | 1 186 | 1 464 | 1 773 | 278 | 1,23 | 309 | 1,21 |
Внеоборотные активы | млн.р. | 276 607 | 412 866 | 466 533 | 136 259 | 1,49 | 53 667 | 1,13 |
Оборотные активы | млн.р. | 192 115 | 226 089 | 246 088 | 33 974 | 1,18 | 19 999 | 1,09 |
Дебиторская задолженность | млн.р. | 20 795 | 55 130 | 101 052 | 34 335 | 2,65 | 45 922 | 1,83 |
Просроченная задолженность | млн.р. | 257 | 72,010 | 295,753 | -185,42 | 0,28 | 223,74 | 4,11 |
Кредиторская задолженность | млн.р. | 28 305 | 40 039 | 41 911 | 11 734 | 1,41 | 1 872 | 1,05 |
Коэффициент текущей ликвидности (1,30) | ед. | 5,60 | 5,65 | 5,87 | 0,02 | 1,00 | 0,22 | 1,04 |
Коэффициент обеспеченности собственными оборотными средствами (0,20) | ед. | 0,66 | 0,69 | 0,74 | 0,03 | 1,05 | 0,05 | 1,07 |
Производственная деятельность предприятия характеризуется опережающим ростом объемов производства в стоимостном выражении над объемами реализации. Это связано с падением покупательского спроса на производимую продукцию. Данное обстоятельство вынуждает идти на снижение цен, и как следствие, ведет к потере части выручки. Так в 2008 году наблюдается 2%-е падение выручки при 7%-ом росте объемов реализации. Это свидетельствует о необходимости снижения темпов роста объемов производства, оптимизации затрат и поиска путей снижения себестоимости.
Одной из наиболее важных и показательных характеристик работы предприятия является размер получаемой прибыли.
Необходимо отметить, что в 2007 году прибыль по сравнению с 2006 увеличилась на 32%. За 2008 год наблюдается значительное падение общей массы прибыли, полученной в результате хозяйственной деятельности МЗХ. Ее объем снизился на 42 831 млн. р., и составил 126 634 млн. р., что ниже прошлогоднего уровня на 25%. В результате этого падения, снизились объемы как чистой, так и нераспределенной прибыли (рисунок 1).
Рисунок 1 – Динамика показателей прибыли, млн. р.
Таким образом, за 2008 год предприятие получило на 40 458 млн. р. или 32,7% меньше чистой прибыли, чем в 2007 году.
Прибыль от реализации продукции в целом по предприятию зависит от трех факторов первого уровня соподчиненности: объема реализации продукции (VPП); полной себестоимости (Сi) и уровня среднереализационных цен (Цi).Для расчета влияния этих факторов на сумму прибыли в 2007 году будем использовать данные таблицы 2.4.
Таблица 2.4 – Данные для факторного анализа прибыли от реализации продукции в 2007 году, млн. р.
Показатель | 2006 | План, пересчитанный на фактический объем реализации | 2007 |
Выручка от реализации продукции за вычетом НДС, акцизного налога и других отчислений из выручки (В) | 540 082 | 568 046 | 698 010 |
Полная себестоимость реализованной продукции (З) | 411 976 | 433 307 | 528 545 |
Прибыль от реализации продукции (П) | 128 106 | 134 739 | 169 465 |
В таблице 2.5 представлены исходные данные факторного анализа прибыли от реализации продукции в 2008 году.
Таблица 2.5 – Данные для факторного анализа прибыли от реализации продукции в 2008 году, млн. р.
Показатель | 2007 | План, пересчитанный на фактический объем реализации | 2008 |
Выручка от реализации продукции за вычетом НДС, акцизного налога и других отчислений из выручки (В) | 698 010 | 727 763 | 732 131 |
Полная себестоимость реализованной продукции (З) | 528 545 | 551 075 | 605 497 |
Прибыль от реализации продукции (П) | 169 465 | 176 689 | 126 634 |
Определим влияние факторов на прибыль от реализации. Результат представим в виде таблицы 2.6.
Таблица 2.6 – Влияние факторов на прибыль от реализации продукции
Фактор | Расчет | Влияние, млн. р. | |
2007 | 2008 | ||
1 | 2 | 3 | 4 |
Объем реализации продукции (VPП) |
2007: 134 739 – 128 106 2008: 176 689 – 169 465 |
6 633 | 7 224 |
Полная себестоимость (Сi) |
2007: 433 307 – 528 545 2008: 551 075 – 605 497 |
- 95 238 | -54 422 |
Уровень среднереализационных цен (Цi) |
2007: 698 010 – 568 046 2008: 732 131 – 727 763 |
129 964 | 4 368 |
Как видно из проведенного анализа, главной причиной сложившейся негативной ситуации явился опережающий рост затрат (118,6%) над темпом роста выручки (109,6%). Виной такого соотношения явились, с одной стороны, рост цен на основные материалы, а с другой, рост амортизационных отчислений после ввода в действие большого количества дорогостоящих основных фондов. Все эти причины повлекли за собой существенное увеличение себестоимости выпускаемой продукции. В свою очередь, снижение покупательского спроса, привело к значительному снижению цен (преимущественно в регионах Российской Федерации), что снизило объем полученной предприятием выручки.
Таким образом, ввиду вышеперечисленных причин, произошло падение прибыльности работы предприятия и, как следствие, снижение показателей рентабельности (рисунок 2).
Рисунок 2 – Динамика различных видов рентабельности, %
Рентабельность реализованной продукции: отражает размер прибыли на рубль затрат на производства и сбыт. На конец 2007 года рентабельность по реализованной продукции составила 20,9%, в то время в 2006 уровень достигал 33,1%.
Рентабельность продаж определяет размер прибыли на рубль реализации. В 2006 году она составляла 23,7%, в 2007 – 24,3%, в 2008 году 16,7 %.
Рентабельность капитала определяет эффективность имущества и составила в 2007 году 28,8 %, в 2008 году 16,3 %
Для более глубокого изучения причин падения рентабельности капитала проведем факторный анализ данного показателя.
Рентабельность активов равна произведению рентабельности продаж и коэффициента оборачиваемости капитала. Таким образам, исходная факторная модель для анализа рентабельности капитала имеет вид [12, стр. 172]:
ROA = Коб ∙ Rрп , (2)
где ROA – рентабельность активов, %;
Коб - коэффициент оборачиваемости, доли ед.;
Rрп – рентабельность продаж, %.
Расчет влияния факторов первого порядка на изменение уровня рентабельности капитала можно произвести методом абсолютных разниц.
Таблица 2.7 - Показатели эффективности использования совокупного капитала
Показатель | 2006 | 2007 | 2008 |
Прибыль от реализации продукции, млн. р. | 128 106,00 | 169 465,00 | 126 634,00 |
Чистая выручка от реализации, млн. р. | 540 082,00 | 698 010,00 | 756 805,00 |
Средняя сумма капитала, млн. р. | 476 230,00 | 588 420,00 | 758 287,00 |
Рентабельность капитала, % | 26,90 | 28,80 | 16,30 |
Рентабельность продаж, % | 23,70 | 24,30 | 16,70 |
Коэффициент оборачиваемости капитала | 1,13 | 1,19 | 0,99 |
Изменение рентабельности капитала за счет: | |||
коэффициента оборачиваемости, % |
|
+ 1,42 | - 4,80 |
рентабельности продукции,% |
|
+ 0,43 | - 7,70 |
ВСЕГО, % | + 1,90 | - 12,50 |
Данные, приведенные в таблице 2.7, показывают, что доходность капитала за 2007 год возросла на 1,9 % (28,8 – 26,9). В связи с ускорением оборачиваемости капитала она возросла на 1,42 %, а за счет некоторого увеличения рентабельности продаж увеличилась на 0,43 %. Однако, в 2008 году падение уровня рентабельности продаж достигло 12,5 %. При этом, за счет снижения оборачиваемости капитала произошло падение рентабельности капитала на 4,8 %, а за счет рентабельности на 7,7 %.
Падение рентабельности продаж и реализации продукции обусловлено, в первую очередь, падением прибыли, а также ростом издержек на производство и сбыт продукции.
В 2007 году среднемесячная заработная плата выросла к уровню 2006 года на 23% (278 тыс. р.). В 2008 году среднемесячная заработная плата выросла к уровню 2007 года на 21% (309 тыс. р.). При этом рост производительности труда работников в 2007 году по сравнению с 2006 составил 30%, а в 2008, по сравнению с 2007, всего семь процентов.
Наращивание объемов выпуска и реализации продукции повлекло за собой естественное увеличение размера оборотных активов, которое составило 18% в 2007 году и 9% в 2008. Однако, не смотря на этот прирост, соотношение оборотных и внеоборотных не претерпело существенных изменений. Это можно объяснить, прежде всего, вводом в действие нового оборудования, что дало прирост и по внеоборотным активам, сохранив практически равновесие в валюте баланса. При этом по внеоборотным активам в 2007 году рост составил 49%, что объясняется вводом в эксплуатацию дорогостоящего оборудования.
Положительно характеризует финансовую стратегию предприятия коэффициент обеспеченности собственными оборотными средствами. К концу 2007 он составил 0,69, а к концу 2008 года он достиг величины 0,74. Такое высокое значение показывает возможность достаточно легко, не используя заемные средства, обеспечить бесперебойную работу предприятия. Прирост этого коэффициента на три – пять процента говорит об эффективной кредитно-финансовой политике предприятия, направленной на сокращение долговых обязательств и вовлечение в оборот большего количества собственных средств, обеспечивая тем самым расширение производственной деятельности.
Некоторые показатели, характеризующие состояние оборотных средств имеют негативную окраску. За истекший период значительно возросла сумма дебиторской задолженности. Ее превышение над кредиторской к концу 2008 года составило 59 108 млн. р. Коэффициент соотношения дебиторской и кредиторской задолженности на конец 2008 года составил 2,41, что превышает уровень 2007 года практически в два раза.
На фоне незначительного прироста кредиторской задолженности сложившаяся ситуация говорит о существенном перетекание абсолютно ликвидных оборотных средств на расчетных счетах в дебиторскую задолженность, что, фактически, свидетельствует о временном извлечении из текущего хозяйственного оборота значительной доли оборотных средств и предоставлении предприятиям-должникам беспроцентного коммерческого кредита.
Для выявления причин такого положения проведем анализ состояния оборотных активов предприятия. Данные таблицы 2.8 показывают, на каких стадиях кругооборота произошло ускорение оборачиваемости капитала, а на каких - замедление.
Таблица 2.8 - Анализ продолжительности оборота оборотного капитала
Показатель | 2006 | 2007 | 2008 | Изменение 06/07 | Изменение 07/08 |
1 | 2 | 3 | 4 | 5 | 6 |
Общая сумма оборотного капитала, млн. р. | 192 115 | 226 089 | 246 088 | 33 974 | 19 999 |
В том числе в: | |||||
производственных запасах | 136 278 | 94 738 | 88 307 | -41 540 | -6 431 |
незавершенном производстве | 13 184 | 11 755 | 12 362 | -1 429 | 607 |
готовой продукции | 4 118 | 12 602 | 13 929 | 8 484 | 1 327 |
дебиторской задолженности | 20 795 | 55 130 | 101 052 | 34 335 | 45 922 |
денежной наличности | 17 740 | 51 864 | 30 438 | 34 124 | -21 426 |
Чистая выручка от реализации продукции, млн. р. | 540 082 | 698 010 | 756 805 | 157 928 | 58 795 |
Общая продолжительность оборота оборотного капитала, дни | 128 | 117 | 117 | -11 | 0 |
В том числе в: | |||||
производственных запасах | 91 | 50 | 42 | -41 | -8 |
незавершенном производстве | 8 | 6 | 6 | -2 | 0 |
готовой продукции | 3 | 6 | 7 | 3 | 1 |
дебиторской задолженности | 14 | 28 | 48 | 14 | 20 |
денежной наличности | 12 | 27 | 14 | 13 | -14 |
В 2006 году структура общей продолжительности оборота оборотного капитала характеризуется значительной продолжительностью нахождения оборотных активов в производственных запасах, что свидетельствует о большой продолжительности производственного цикла (рисунок 3).
Рисунок 3 – Структура общей продолжительности оборота оборотного капитала в 2006 году, дни
В 2007 году значительно уменьшилась продолжительность нахождения капитала в производственных запасах, что свидетельствует о сокращении производственного цикла. Вместе с тем постоянно увеличивается продолжительность периода обращения средств в готовой продукции и дебиторской задолженности (рисунок 4).
Рисунок 4 – Структура общей продолжительности оборота оборотного капитала в 2007 году, дни
В 2008 году произошел значительный рост периода обращения оборотного капитала в дебиторской задолженности, что свидетельствует об извлечении средств из оборота (рисунок 5).
Рисунок 5 – Структура общей продолжительности оборота оборотного капитала в 2008 году, дни
Продолжительность оборота, как всех текущих активов, так и отдельных видов (Поб), может измениться за счет суммы выручки (В) и средних остатков оборотных средств (Ост). Для расчета влияния данных факторов используется способ цепной подстановки.
Для 2007 года:
Поб2006 = Ост2006 ∙ 360 / В2006 = 192 115 ∙ 360 / 540 082 = 128 дней
Побусл = Ост2007 ∙ 360 / В2006 = 226 089 ∙ 360 / 540 082 = 151 дня
Поб2007 = Ост2007 ∙ 360 / В2007 = 226 089 ∙ 360 / 698 010 = 117 дней
Для 2008 года:
Поб2007 = Ост2007 ∙ 360 / В2007 = 226 089 ∙ 360 / 698 010 = 117 дней
Побусл = Ост2008
∙ 360 / В2007 = 246 088360
/ 698 010 = 127 дней
Поб2008 =
Ост2008 ∙ 360 / В2008 = 246 088 360
/ 756 805 = 117 дней
Отсюда изменение продолжительности оборота оборотного капитала за счет (млн. р.): | |||
2006/07 | 2007/08 | ||
суммы оборотного капитала |
Поб2007 - Побусл |
-34,00 | -10,00 |
остатков оборотного капитала |
Побусл - Поб2006 |
23,00 | 10,00 |
в т.ч. за счет остатков в: | |||
производственных запасах |
(ПЗ1 – ПЗ0) |
-27,69 | -3,32 |
незавершенном производстве |
(НП1 – НП0) ∙ 360 / В0 |
-0,95 | 0,31 |
готовой продукции |
(ГП1 – ГП0) ∙ 360 / В0 |
5,66 | 0,68 |
дебиторской задолженности |
(ДЗ1 – ДЗ0) ∙ 360 / В0 |
22,89 | 23,68 |
денежной наличности |
(ДН1 – ДН0) ∙ 360 / В0 |
22,75 | -11,05 |
Экономический эффект в результате ускорения оборачиваемости капитала выражается в относительном высвобождении средств из оборота, а также в увеличении суммы выручки и суммы прибыли.
Сумма высвобожденных средств из оборота в связи с ускорением или дополнительно привлеченных средств в оборот при замедлении оборачиваемости капитала определяется умножением однодневного оборота по реализации на изменение продолжительности оборота [12, стр. 158].
,
(3)
где
-
Сумма
высвобожденных средств из оборота в связи с ускорением (-Э) или дополнительно
привлеченных средств в оборот (+Э) при замедлении оборачиваемости капитала,
млн. р.
Отсюда:
Э2006/07 = 698 010 / 360 ∙ (117 - 128) = - 21 328 млн. р.
Э2007/08 = 756 805 / 360 ∙ (117 - 117) = 0 млн. р.
Таким образом, в связи с ускорением оборачиваемости оборотного капитала в 2007 году на одиннадцать дней произошло относительное высвобождение средств из оборота на сумму 21 328 млн. р. В 2008 году изменений в оборачиваемости оборотного капитала не произошло.
Чтобы установить влияние коэффициента оборачиваемости на изменение суммы чистой выручки, можно использовать следующую факторную модель [12, стр. 95]:
В = KL ∙ Кобо , (4)
где В - чистая выручка от реализации продукции, млн. р.;
KL - общая сумма оборотного капитала, млн. р.;
Кобо - коэффициент оборачиваемости оборотного капитала (частное от деления чистой выручки на общую сумму оборотного капитала), ед.
Отсюда:
Вkоб = КL2007 ∙
Кобо =
226 089 ∙ (3,09 – 2,81) =
62 883 млн. р.
ВкL =
KL ∙
Кобо2006
= (226 089 - 192 115) ∙ 2,81
= 95 045 млн. р.
Вобщ = В2007 – B2006
= 698 010 - 540 082 = 157 928 млн. р.
Вkоб
= КL2008
∙
Кобо =
246 088 ∙ (3,08
– 3,09) = - 2 948 млн. р.
ВкL =
KL ∙
Кобо2007
= (246 088 - 226 089) ∙ 3,09
= 61 743 млн. р.
Вобщ = В2008 – B2007
= 756 805 - 698 010 = 58 795 млн. р.
Увеличение коэффициента оборачиваемости оборотного капитала в 2007 году произошло благодаря опережающему росту чистой выручки от реализации над общей стоимостью оборотного капитала. В 2008 году темпы роста выручки упали ниже уровня роста оборотного капитала, что обусловило падение коэффициента оборачиваемости и, соответственно, предприятие понесло убытки в размере 2 948 млн. р. из чистой выручки. Однако негативное влияние изменения коэффициента оборачиваемости в 2008 году не вызвало падение общего уровня чистой выручки т.к. было нивелировано благоприятным изменением структуры капитала.
Увеличение суммы прибыли за счет изменения коэффициента оборачиваемости капитала можно рассчитать умножением прироста последнего на базовый уровень коэффициента рентабельности продаж и на фактическую среднегодовую сумму оборотного капитала [12, стр. 108].
П =
Кобо ∙ Rpn0
∙
КL1
, (5)
где П – изменение суммы прибыли, млн.
р.;
Rpn0 - базовый уровень коэффициента рентабельности продаж, доли ед.;
КL1 - фактическая среднегодовая сумма оборотного капитала, млн. р.
П2006/07 =
Кобо ∙
Rpn2006
∙
КL2007
= 0,28 ∙
0,237
∙
226 089
= 15 003 млн. р.
П2007/08 =
Кобо ∙
Rpn2007
КL2008
= - 0,01∙
0,243
∙ 246 088
= - 597 млн. р.
По результатам анализа в 2007 году за счет ускорения оборачиваемости оборотного капитала предприятие дополнительно получило прибыли на сумму 15 003 млн. р., а в 2008 году за счет замедления оборачиваемости оборотного капитала предприятие понесло из прибыли убытки в размере 597 млн. р.
2.4 Анализ себестоимости продукции
Важным показателем, характеризующим работу предприятий, является себестоимость продукции, работ и услуг. Анализ себестоимости продукции, работ и услуг имеет большое значение. Он позволяет выяснить тенденции изменения данного показателя, выполнения плана по его уровню, определить влияние факторов на его прирост, установить резервы и дать оценку работы предприятия по использованию возможностей снижения себестоимости продукции.
Исходя из определенных в первом разделе показателей себестоимости, объектами анализа являются:
– затраты на рубль объема произведенной продукции;
– полная себестоимость объема произведенной продукции в целом и по элементам затрат;
– себестоимость отдельных изделий.
Начнем анализ с динамики затрат на производство продукции
2.4.1 Анализ динамики изменения затрат на производство Динамика затрат на производство представлена в таблице 2.9.
Таблица 2.9 – Динамика затрат на производство
Показатель | 2006 год | 2007 год | 2008 год | ||||
млн. р. | Затраты на рубль объема произведенной продукции, р. | млн. р. | Затраты на рубль объема произведенной продукции, р. | млн. р. | Затраты на рубль объема произведенной продукции, р. | ||
1 | 2 | 3 | 4 | 5 | 6 | 7 | |
Объем произведенной продукции | |||||||
- в сопоставимых ценах | 409 999 | 668 896 | 716 733 | ||||
- в фактических ценах | 486 827 | 635 766 | 682 800 | ||||
Себестоимость объема произведенной продукции, в т.ч. | 361 867 | 0,740 | 464 512 | 0,736 | 550 719 | 0,807 | |
Материальные затраты | 273 253 | 0,559 | 364 621 | 0,574 | 422 231 | 0,618 | |
из них: | |||||||
основные материалы, сырье | 107 997 | 0,221 | 123 140 | 0,194 | 137 379 | 0,201 | |
покупные комплектующие, кооперация | 146 214 | 0,299 | 216 278 | 0,34 | 252 400 | 0,370 | |
вспомогательные материалы | 11 038 | 0,023 | 13 841 | 0,022 | 19 451 | 0,028 | |
топливо, энергия | 8 003 | 0,020 | 11 362 | 0,018 | 13 001 | 0,019 | |
Расходы на оплату труда | 35 787 | 0,074 | 44 240 | 0,07 | 53 570 | 0,078 | |
Отчисления на социальные нужды | 24 138 | 0,050 | 17 414 | 0,027 | 21 312 | 0,031 | |
Амортизация | 13 857 | 0,028 | 17 425 | 0,027 | 25 558 | 0,037 | |
Прочие денежные расходы | 14 831 | 0,030 | 20 813 | 0,033 | 28 048 | 0,041 | |
из них: | |||||||
прочие налоги и отчисления | 7 033 | 0,010 | 9 700 | 0,015 | 11 204 | 0,016 | |
расходы на гар.ремонт | 553 | 0,000 | 512 | 0,001 | 1 544 | 0,002 | |
прочие расходы | 7 245 | 0,010 | 10 601 | 0,017 | 15 300 | 0,022 |
Динамика структуры затрат представлена в таблице 2.10.
Таблица 2.10 – Динамика структуры затрат на производство
Показатель | Отклонение | Уд. вес в себестоимости, % | Отклонение по затратам на рубль объема произведенной продукции, % | ||||||
2006/07 | 2007/08 | ||||||||
млн. р. | % | млн. р. | % | 2006 г. | 2007 г. | 2008 г. | 2006/07 | 2007/08 | |
1 | 2 | 3 | 4 | 5 | 6 | 7 | 8 | 9 | 10 |
Себестоимость объема произведенной продукции, в т.ч.: | 102 645 | 128,37 | 86 207 | 118,56 | 100,00 | 100,00 | 100,00 | -0,009 | 0,076 |
Материальные затраты | 91 368 | 133,44 | 57 610 | 115,80 | 75,51 | 78,50 | 76,67 | 0,015 | 0,044 |
из них: | |||||||||
основные материалы, сырье | 15 143 | 114,02 | 14 239 | 111,56 | 29,84 | 26,51 | 24,95 | -0,027 | 0,007 |
покупные комплектующие, кооперация | 70 064 | 147,92 | 36 122 | 116,70 | 40,41 | 46,56 | 45,83 | 0,041 | 0,030 |
вспомогательные материалы | 2 803 | 125,39 | 5 610 | 140,53 | 3,05 | 2,98 | 3,53 | -0,001 | 0,006 |
топливо, энергия | 3 359 | 141,97 | 1 639 | 114,42 | 2,21 | 2,45 | 2,36 | 0,002 | 0,001 |
Расходы на оплату труда | 8 453 | 123,62 | 9 330 | 121,09 | 9,89 | 9,52 | 9,73 | -0,004 | 0,008 |
Отчисления на социальные нужды | -6 724 | 72,14 | 3 898 | 122,39 | 6,67 | 3,75 | 3,87 | -0,023 | 0,004 |
Амортизация | 568 | 125,75 | 8 133 | 146,67 | 3,83 | 3,75 | 4,64 | -0,001 | 0,010 |
Прочие денежные расходы | 5 982 | 140,33 | 7 235 | 134,76 | 4,10 | 4,48 | 5,09 | 0,003 | 0,008 |
В 2008 году объём произведенной продукции в фактических оптовых ценах составил 682 800 млн. р., в 2007 году – 635 766 млн. р., в 2006 - 486 827 млн.р. Темп роста в 2007 году составил – 130,59 %, в 2008 - 107,40 %
Себестоимость объема произведенной продукции за 2008 год сложилась в размере 550 719 млн. р., за 2007 год – 464 512 млн. р., в 2006 году - 361 867 млн. р. Темп роста в 2008 году составил 118,56 %, а в 2007 – 128,37 %.
Ежегодно увеличиваются расходы по всем элементам затрат, особенно интенсивный рост наблюдается по материальным затратам, которые имеют в структуре себестоимости наибольший удельный вес (рисунок 6).
Рисунок 6 Диаграмма роста затрат на производство, млн. р.
В разрезе статьи «Материальные затраты» расходы распределились следующим образом (таблица 2.11):
Таблица 2.11 – Структура расходов в разрезе статьи «Материальные затраты»
Элемент затрат | 2006 г. | 2007 г | 2008 г. | Отклонение (2006/07) | Отклонение (2007/08) | ||||||
Млн. р. | Удельный вес, доли | Млн. р. | Удельный вес, доли | Млн. р. | Удельный вес, доли | Млн. р. | Удельный вес, доли | Млн. р. | Удельный вес, доли | ||
1 | 2 | 3 | 4 | 5 | 6 | 7 | 8 | 8 | 10 | 11 | |
Сырьё и материалы | 97 168 | 0,36 | 107 833 | 0,39 | 120 375 | 0,33 | 10 665 | 0,03 | 12 542 | -0,06 | |
Транспортные расходы | 2 905 | 0,01 | 4 431 | 0,02 | 5 372 | 0,01 | 1 526 | 0,01 | 941 | -0,01 | |
Таможенные услуги | 7 924 | 0,03 | 10 876 | 0,04 | 11 632 | 0,03 | 2 952 | 0,01 | 756 | -0,01 | |
Покупные и комплектующие | 146 214 | 0,54 | 216 278 | 0,79 | 252 400 | 0,69 | 70 064 | 0,25 | 36 122 | -0,10 | |
Вспомогательные материалы | 11 038 | 0,04 | 13 841 | 0,05 | 19 451 | 0,05 | 2 803 | 0,01 | 5 610 | 0,00 | |
Топливо, энергия | 8 004 | 0,03 | 11 362 | 0,04 | 13 001 | 0,04 | 3 358 | 0,01 | 1 639 | 0,00 | |
Рост затрат по материалам, покупным и комплектующим изделиям вызван ростом объёма производства на 7,41%, изменением структуры изготовленной продукции, а также увеличением цен в валюте поставщика закупаемого сырья и материалов.
Доля импортного сырья и материалов, используемых в производстве на МЗХ, составляет 56% .
В 2007 году среднемесячная заработная плата выросла к уровню 2006 года на 23% (555 тыс. р.). В 2008 году среднемесячная заработная плата выросла к уровню 2007 года на 21% (619 тыс. р.). При этом рост производительности труда работников в 2007 году по сравнению с 2006 составил 30%, а в 2008, по сравнению с 2007, всего 7%. Таким образам в 2008 году наблюдался опережающий рост оплаты труда по сравнению с ростом производительности, что является негативным явлением в работе предприятия.
Увеличение амортизационных отчислений связано с вводом в эксплуатацию нового оборудования. Увеличение удельного веса прочих расходов в себестоимости связано с увеличением затрат на текущий и капитальный ремонт зданий и сооружений общепроизводственного назначения, проведением пусконаладочных работ, связанных с вводом нового оборудования, силами подрядных организаций и использованием привлеченного транспорта.
2.4.2 Факторный анализ себестоимости продукции
Общая сумма затрат может измениться из-за объема выпуска продукции в целом по предприятию, уровня переменных затрат на единицу продукции и суммы постоянных расходов на весь выпуск продукции. Таким образом, факторная модель для анализа общей суммы затрат примет вид [12, стр. 225]:
,
(6)
где Зобщ – общая сумма затрат, млн. р.;
VВПобщ – объем выпуска продукции, млн. р.;
В – уровень переменных затрат на единицу продукции, млн. р.;
А – уровень постоянных затрат, млн. р.
Данные для расчета влияния этих факторов приведены в таблице 2.12 и таблице 2.13.
Таблица 2.12 – Данные для факторного анализа общей суммы затрат на производство продукции в 2007 году, млн. р.
Затраты | 2006/2007 | |||
Сумма, млн. р. | Факторы изменения затрат | |||
Объем выпуска продукции, шт. | Переменные затраты, млн. р. | Постоянные затраты, млн. р. | ||
По плану на плановый выпуск продукции |
359 032 | 897 340 | 0,24 | 143 670 |
По плановому уровню на фактический выпуск продукции |
375 341 | 965 294 | 0,24 | 143 670 |
Фактические при плановом уровне постоянных затрат |
442 911 | 965 294 | 0,31 | 143 670 |
Фактические |
468 305 | 965 294 | 0,31 | 169 064 |
Таблица 2.13 Данные для факторного анализа общей суммы затрат на производство продукции в 2008 году, млн. р.
Затраты | 2007/2008 | |||
Сумма, млн. р. | Факторы изменения затрат | |||
Объем выпуска продукции, шт. | Переменные затраты, млн. р. | Постоянные затраты, млн. р. | ||
По плану на плановый выпуск продукции |
468 305 | 965 294 | 0,31 | 169 064 |
По плановому уровню на фактический выпуск продукции |
481 082 | 1 006 509 | 0,31 | 169 064 |
Фактические при плановом уровне постоянных затрат |
531 407 | 1 006 509 | 0,36 | 169 064 |
Фактические |
553 390 | 1 006 509 | 0,36 | 191 047 |
Из-за повышения уровня удельных переменных затрат рост издержек на производство продукции составил 67 570 млн. р. (442 911 – 375 341) в 2007 году и 50 325 млн. р. (531 407 – 481 082) в 2008 году.
Постоянные расходы возросли в 2007 году по сравнению с 2006 на 25 394 млн. р., а в 2008 году по сравнению с 2007 на 21 983 млн. р., что также послужило одной из причин увеличения общей суммы затрат.
Таким образом, общая сумма затрат в 2007 году выше уровня 2006 на 109 273 млн. р. (468 305 - 359 032), или +30 %, а в 2008, по сравнению с 2007 на 85 085 млн. р.(553 390 - 468 305), или +18 %. За счет увеличения объема производства продукции она возросла в 2007 на 16 309 млн. р. (375 341 - 359 032), в 2008 на 12 777 млн. р. (481 082 - 468 305). За счет роста себестоимости продукции произошло увеличение издержек - на 92 964 млн. р. (464 512 - 428 622), или на 24,77 % в 2007 году. В 2008 году вклад роста себестоимости в рост издержек производства составил 72 308 млн. р., или 15,03 %.
Важный обобщающий показатель себестоимости продукции – затраты на рубль объема произведенной продукции, который выгоден тем, что, во-первых, очень универсальный: может рассчитываться в любой отрасли производства, и, во-вторых, наглядно показывает прямую связь между себестоимостью и прибылью. Определяется он отношением, общей суммы затрат на производство и реализацию продукции к стоимости произведенной продукции в действующих ценах.
Влияние факторов первого уровня на изменение затрат на рубль товарной продукции рассчитывается способом цепной подстановки по данным таблиц 2.12, 2.13 и по данным о выпуске товарной продукции (таблица 2.14).
Таблица 2.14 – Объем произведенной продукции, млн. р.
Объем произведенной продукции | Формула | 2006/2007 | 2007/2008 |
По плану |
|
487 256 | 636 129 |
Фактически по ценам плана |
|
524 155 | 663 289 |
Фактически по фактическим ценам |
|
636 129 | 682 413 |
Расчет влияния факторов на изменение затрат на рубль произведенной продукции представлен в таблицах 2.15, 2.16.
Таблица 2.15 Анализ затрат на рубль произведенной продукции в 2007 г.
Затраты на рубль произведенной продукции, млн. р. | Фактор (2006/2007) | |||||
Объем производства, шт. | Удельные переменные издержки, млн. р. | Сумма постоянных издержек, млн. р. | Отпускные цены на продукцию, млн. р. | |||
план | 359 032 / 487 256 | 0,74 | 897 340,00 | 0,24 | 143 670,00 | 0,543 |
усл.1 | 375 341 / 524 155 | 0,72 | 965 294,00 | 0,24 | 143 670,00 | 0,543 |
усл.2 | 442 911 / 524 155 | 0,85 | 965 294,00 | 0,31 | 143 670,00 | 0,543 |
усл.3 | 468 305 / 524 155 | 0,89 | 965 294,00 | 0,31 | 169 064,00 | 0,543 |
факт | 468 305 / 636 129 | 0,74 | 965 294,00 | 0,31 | 169 064,00 | 0,659 |
Δобщ = 0,74 – 0,74 = 0,00 коп. | - 0,02 | + 0,13 | + 0,04 | - 0,150 |
Аналитические расчеты показывают, что в 2007 году предприятие сохранило затраты на рубль произведенной продукции неизменными. Это произошло благодаря росту отпускных цен на продукцию, который составил 0,15 коп (0,74 – 0,89) и одновременным увеличением переменных издержек на 0,13 коп.
Таблица 2.16 – Анализ затрат на рубль произведенной продукции в 2008 г.
Затраты на рубль произведенной продукции, млн. р. | Фактор (2007/2008) | |||||
Объем производства, шт. | Уровень удельных переменных издержек, млн. р. | Сумма постоянных издержек, млн. р. | Отпускные цены на продукцию, млн. р. | |||
план | 468 305 / 636 129 | 0,74 | 965 294,00 | 0,31 | 169 064,00 | 0,659 |
усл.1 | 481 082 / 663 289 | 0,73 | 1 006 509,00 | 0,31 | 169 064,00 | 0,659 |
усл.2 | 531 407 / 663 289 | 0,80 | 1 006 509,00 | 0,36 | 169 064,00 | 0,659 |
усл.3 | 553 390 / 663 289 | 0,83 | 1 006 509,00 | 0,36 | 191 047,00 | 0,659 |
факт | 553 390 / 682 413 | 0,81 | 1 006 509,00 | 0,36 | 191 047,00 | 0,678 |
Δобщ = 0,81 – 0,74 = + 0,07 коп. | - 0,01 | + 0,07 | + 0,03 | - 0,020 |
В 2008 году произошло увеличение уровня затрат на рубль продукции на 0,07 копейки. Увеличение обусловлено ростом переменных и постоянных издержек (на 0,07 и 0,03 коп. соответственно). Увеличение отпускных цен на 0,02 коп. не смогло нивелировать увеличения затрат.
Таким образом, проведенный анализ свидетельствует о росте затрат на производство за счет высокой ресурсоемкости производства и увеличения стоимости ресурсов. Единственным источником снижения затрат остается увеличение отпускных цен, что в сложившейся экономической обстановке является нецелесообразным. Данные факты свидетельствуют о необходимости поиска внутренних резервов для снижения себестоимости выпускаемой продукции.
Чтобы установить влияние исследуемых факторов на изменение суммы прибыли, необходимо абсолютные приросты затрат на рубль произведенной продукции за счет каждого фактора умножить на фактический объем реализации продукции, выраженный в плановых ценах
Влияние факторов на изменение уровня себестоимости единицы продукции изучают с помощью факторной модели [12, стр. 231]:
,
(7)
где С - себестоимость единицы продукции, тыс. р.
Данные, необходимые для анализа уровня себестоимости единицы продукции представлены в таблице 2.17.
Таблица 2.17 – Данные для факторного анализа себестоимости изделия
Показатель | 2006 | 2007 | 2008 | Отклонение | |
2006/2007 | 2007/2008 | ||||
Объем производства, шт. | 897 340 | 965 294 | 1 006 509 | 67 954 | 41 215 |
Сумма постоянных затрат, млн. р. | 143 670 | 169 064 | 191 047 | 25 394 | 21 983 |
Сумма удельных переменных затрат, тыс. р. | 240 | 310 | 360 | 70 | 50 |
Себестоимость одного изделия, тыс. р. | 400 | 485 | 550 | 85 | 65 |
Используя факторную модель и данные таблицы 2.17, произведем расчет влияния факторов на изменение себестоимости отдельного изделия методом цепной подстановки:
=
143 670 000 / 897 340 + 240 = 400 тыс. р.
=
143 670 000 / 965 294 + 240 = 389 тыс. р.
=
169 064 000 / 965 294 + 240 = 415 тыс. р.
=
169 064 000 / 965 294 + 310 = 485 тыс. р.
=
169 064 000 / 1 006 509 + 310 = 478 тыс. р.
=
191 047 000 / 1 006 509 + 310 = 500 тыс. р.
=
191 047 000 / 1 006 509 + 360 = 550 тыс. р.
Общее изменение себестоимости единицы продукции составляет:
ΔСобщ(2006/07) = С2007 – С2006 = 485 - 400 = + 85 тыс. р.
ΔСобщ(2007/08) = С2008 – С2007 = 478 - 485 = + 65 тыс. р.
В том числе за счет:
объема производства продукции:
ΔСVвп(2006/07) = Сусл.1.1 – С2006 = 389 - 400 = - 11 тыс. р.
ΔСVвп(2007/08) = Сусл.2.1 – С2007 = 478 - 485 = - 7 тыс. р.
суммы постоянных затрат:
ΔСА (2006/07) = Сусл.1.2 – С усл.1.1 = 415 - 389 = + 26 тыс. р.
ΔСА (2007/08) = Сусл.2.2 – С усл.2.1 = 500 - 478 = + 22 тыс. р.
суммы удельных переменных затрат:
ΔСB (2006/07) = С2007 – С усл.1.2 = 485 - 415 = + 70 тыс. р.
ΔСB (2007/08) = С2008 – С усл.2.2 = 550 - 500 = + 50 тыс. р.
Таким образом, в результате проведенного анализа организационной структуры и данных о производственно-хозяйственной деятельности предприятия, были выявлены следующие проблемы:
– отсутствие в организационной структуре отдела, являющегося интегрирующим центром работы по учету, анализу и контролю затрат предприятия, в том числе и себестоимости производимой продукции;
– отсутствие на предприятии комплексной системы управления себестоимостью продукции;
– преимущественный рост себестоимости продукции за счет материальных затрат. Исходя из значительных объемов производства, даже небольшое сокращение затрат сырья и материалов на единицу продукции может дать ощутимый экономический эффект.
3 ПУТИ СНИЖЕНИЯ СЕБЕСТОИМОСТИ ПРОДУКЦИИ НА МЗХ ЗАО «АТЛАНТ»
3.1 Организационно-экономические мероприятия по усовершенствованию процесса управления затратами
Как отмечалось во втором разделе, для решения выявленных в результате анализа проблем, предлагается использовать комплексные мероприятия, в частности, набирающую популярность в последние годы концепцию «Бережливое производство».
Практически все предприятия машиностроительного комплекса являются исключительно материалоемкими. Исходя из значительных объемов производства, даже небольшое сокращение затрат сырья и материалов на единицу продукции может дать ощутимый экономический эффект. Данная цель может быть достигнута только при условии существования эффективно налаженной системы учета и контроля затрат. Одним из вариантов решения данной, и не только, проблемы может стать смена концепции менеджмента. Предлагается переход к нелинейной концепции, например «Бережливое производство» (БП). Преимуществом данного метода является то, что система на 80% состоит из организационных мер и лишь 20% составляют инвестиции в технологию.
Бережливое производство — логистическая концепция менеджмента, сфокусированная на оптимизации бизнес-процессов с максимальной ориентацией на рынок и с учётом мотивации каждого работника. Бережливое производство составляет основу новой философии менеджмента и является одной из форм нелинейного менеджмента.
Основные принципы БП [2, стр. 12]:
– превосходное качество (сдача с первого предъявления, система ноль дефектов, обнаружение и решение проблем у истоков их возникновения);
– минимизация потерь путем устранения всех видов деятельности, которые не приносят добавочной стоимости заказчику, максимальное использование всех ресурсов (капитал, люди, земля);
– гибкость;
– установление долговременных отношений с заказчиком (путем деления рисков, затрат и информации);
– самоорганизация, эволюция, адаптация.
Целями внедрения системы «Бережливое производство» являются:
– мининимизация трудозатрат,
– минимизация сроков создания новой продукции,
– гарантия поставки продукции заказчику,
– максимальное качество при минимальной стоимости.
Основными инструментами системы «Бережливое производство» являются:
– визуализация и стандартизация рабочего места (5S);
– диагностика производственного процесса (VSM);
– управление потоками (TFM);
– снижение межоперационных запасов (Kanban);
– всеобщее обслуживание оборудования (TPM);
– технология быстрой переналадки (SMED);
– система встроенного качества (TQM).
На мой взгляд, исследуемое предприятие на данный момент не обладает достаточными ресурсами для проведения полноценной работы по внедрению предлагаемой концепции. Поэтому на первоначальном этапе предлагаю использовать альтернативные инструменты в рамках системы «Бережливое производство». В качестве таких инструментов будут выступать «Целевое планирование затрат» и «Операционно-ориентированный метод калькуляции себестоимости».
Концепция БП направлена на уменьшение семи видов потерь, которые частично ложатся и на себестоимость продукции:
– перепроизводство товаров, т.е. производство товаров, на которые еще не возник спрос;
– ожидание следующей производственной стадии;
– ненужная транспортировка;
– лишние этапы обработки, требующихся из-за недостатка оборудования, несовершенства проекта, ненужной инициативы;
– наличие любых, кроме минимально необходимых, запасов;
– ненужные перемещения людей в ходе работы (в поисках деталей, инструментов);
– производство брака.
Во втором разделе были проанализированы организационная структура предприятия и функции отдела планирования и экономического анализа. Как видно, функции управления затратами, и себестоимостью в частности, размыты. Очевидно, что для проведения коренных изменений необходим координационный центр. Именно для выполнения задач центра по учету, управлению и анализу затрат предлагаю создать отдел контроллинга.
3.1.1 Совершенствование организационной структуры управления затратами
Для реализации концепции бережливого производства необходимо наладить эффективную аналитическую работу. На МЗХ ЗАО «Атлант» аналитикой традиционно занимается отдел планирования и экономического анализа. Однако данная работа является не приоритетной, и большая часть времени работы отдела приходится на решение текущих вопросов. В то же время, кроме анализа и констатации текущего положения дел на предприятии, должна проводиться непрерывная работа по улучшению экономической деятельности. Для реализации данной цели считаю необходимым организацию отдела контроллинга.
Информация, которую готовит служба контроллинга, предназначена для заместителя директора по экономике и финансам, а также для генерального директора. Считаю целесообразным подчинить ее напрямую заместителю директора по экономике и финансам, т.к. ему непосредственно подчинены начальники финансового отдела и отдела планово-экономического анализа. Таким образом, начальник службы контроллинга получит достаточно высокий статус и независимость от начальников других финансово-экономических служб.
Проектируемая служба контроллинга состоит из пяти сотрудников (контроллеров) с определенными должностными обязанностями. Считаю, что оптимальным будет следующий состав службы:
а) начальник службы контроллинга;
Начальник службы контроллинга несет ответственность за выходящие документы, аналитические расчеты и прогнозы перед своим непосредственным начальником - заместителем директора по экономике и финансам.
б) контроллер — куратор цехов;
В связи с большими объемами информации, на данной должности должны работать два специалиста. Один будет ответственен за цеха основного производства, другой — вспомогательного. В обязанности контроллера — куратора цехов входит:
– разработка форм сбора аналитической информации по цехам;
– сбор аналитической (плановой и фактической) информации от цехов (центров ответственности);
– обработка и анализ полученных данных, разработка нормативов затрат по цехам и поддержание их актуальности;
– расчет аналитических показателей работы цехов и предприятия в целом;
– анализ отклонений фактических данных от плановых, выявление причин отклонения;
– составление аналитических отчетов для заместителя генерального директора по экономике и финансам;
– экспертиза управленческих решений, связанных с затратами курируемых цехов.
в) контроллер — специалист по управленческому учету;
В сферу деятельности данного специалиста входит работа с бухгалтерией и получение аналитических данных из учетных регистров.
Обязанности контроллера — специалиста по управленческому учету:
– разработка процедур передачи данных из бухгалтерии в службу контроллинга;
– контроль сбора и анализа фактической учетной информации;
– разработка предложений по оптимизации учетного процесса в бухгалтерии с позиции аналитической службы;
– экономическая экспертиза управленческих решений.
г) контроллер — специалист по информационным системам.
Обязанности контроллера — специалиста по информационным системам:
– оценка целесообразности автоматизации контроллинговой работы на отдельных этапах;
– оценка вариантов и предложений по автоматизации контроллинговой работы;
– расчеты и обоснование затрат на автоматизацию контроллинговой работы;
– разработка форм для автоматизированного сбора информации;
– оптимизация документооборота на предприятии;
– координация работы отдела автоматизации в области автоматизации контроллинговой работы;
– оценка качества систем автоматизации финансово-хозяйственной деятельности и выработка предложений по улучшению их работы.
Представленные должности являются достаточно специализированными. На должность куратора цехов целесообразно приглашать экономистов цехов, экономистов планово-экономического отдела, финансового отдела. Основным требованием, предъявляемым к специалисту по управленческому учету, является теоретическое и практическое знание бухгалтерского учета, особенностей и недостатков учета на данном предприятии. Данную работу целесообразно поручить специалисту из бухгалтерии. Контроллер — специалист по информационным системам — квалифицированный сотрудник из отдела информационных технологий, отдела общего делопроизводства детально знающий документооборот на предприятии и способный поставить задачу автоматизации контроллинговой работы.
Именно данное подразделение будет «проводником» в процессе внедрения БП.
Оценим экономический эффект от организации отдела контроллинга. Расчет представим в виде таблицы 3.1.
Таблица 3.1Экономический эффект от организации отдела контроллинга
Функциональная область | Эффект | Стоимостная оценка, тыс. р. |
1 | 2 | 3 |
Планирование | увеличение оборачиваемости средств | 5 030 640 |
сокращение объемов кредитных ресурсов | 1 257 330 | |
доход от высвободившихся ресурсов | 563 317 | |
Учет | экономия на предотвращении вероятных убытков, неэффективного отвлечения средств | 637 518 |
Анализ Консалтинг |
экономия от предотвращения негативных отклонений | 210 563 |
Контроль | избегание штрафных санкций | 6 544 |
сокращение операционных издержек | 709 106 | |
Мониторинг | дополнительная прибыль | 1 207 379 |
Интеграция Координация |
стоимость высвободившихся экономических ресурсов (трудовых, финансовых и т. п.) при повышении производительности труда | 817 350 |
ИТОГО | 10 439 747 |
Организация нового отдела требует определенных затрат. Источники данных затрат и их стоимостная оценка представлены в таблице 3.2.
Таблица 3.2 – Затраты на организацию отдела контроллинга
Источник затрат |
Стоимостная оценка, тыс. р. |
Модернизация системы управленческого учета и бюджетирования на предприятии | 5 584 690 |
Модернизация информационных систем | 1 560 012 |
Выплата вознаграждения сотрудникам за дополнительный объем работ | 108 000 |
Услуги привлеченных специалистов (контролеров) | 144 000 |
Обучение сотрудников | 14 700 |
ИТОГО | 7 411 402 |
Таким образом, чистый годовой экономический эффект от организации отдела контроллинга составит 3 028 345 тыс. р.
Типовыми задачами службы контроллинга являются:
– организация, координация и методическая поддержка процессов планирования и бюджетирования на предприятии;
– организация, координация и методическая поддержка системы учета затрат и доходов на предприятии.
Очевидно, что отдел, специализирующийся на управлении затратами, должен иметь современный методологический аппарат для выполнения своих задач. В связи с этим я предлагаю в качестве основного инструмента управления затратами использовать систему «target costing» («система целевого планирования затрат»).
3.1.2 Совершенствование методологии управления затратами
Целевое планирование затрат (Target Costing) - средство управления затратами, применяемое для снижения любых затрат, связанных с продуктом в течение всего периода его жизненного цикла, путем объединения усилий производственных, конструкторских, исследовательских, маркетинговых, экономических подразделений компании
Основу концепции составляет изменение взгляда на взаимозависимость цены, прибыли и себестоимости:
Целевая себестоимость = Целевая цена - Целевая прибыль
Таким образом, основным условием для расчетов являются цена, по которой можно осуществить продажи в планируемых объемах, и прибыль, уменьшение суммы которой лишает смысла работы над этим продуктом. Итогом расчетов является себестоимость, в которую необходимо вписаться при разработке, производстве и продвижении продукта.
Процесс обычного подхода к расчету себестоимости проводится в две-три полных итерации и редко приводит к оптимальному результату. Подход к управлению себестоимостью продукции при целевом планировании затрат предполагает более короткий итерационный блок, в ходе которого происходит балансировка свойств продукта с требованиями и ценами рынка. Появляются новые инструменты управления и точки фокусирования внимания.
МЗХ ЗАО «Атлант» представляет собой предприятие, на котором десятилетиями складывалась практика работы в рамках традиционных подходов к себестоимости разрабатываемых и уже запущенных в производство изделий. Поэтому при обновлении системы управления затратами необходимо пройти определенную последовательность шагов (таблица 3.3).
Таблица 3.3– Расчет затрат на внедрение целевого планирования затрат
Этап | Мероприятия | Затраты, тыс.р. |
1 | 2 | 3 |
Формирование у менеджмента предприятия понимания необходимости перехода к системе целевого планирования затрат и приоритета рыночных цен товара. | Обучение сотрудников | Учтено в разделе 3.1 |
Создание команды поддержки внедрения. | ||
Конкретизация методологии целевого планирования затрат с учетом особенности предприятия. | Составление модели затрат продукта для анализа альтернатив в целях подготовки необходимых для принятия решений данных. | 25 534,807 |
Определение показателей целевой себестоимости для видов продукции предприятия, основываясь на анализе рыночных ниш, понимании требований потребителей, оценке драйверов затрат, возможных компромиссов между затратами и требованиями к товару, определении эластичности спроса, анализе соотношений объемов и затрат. | ||
Изменения в организации производства, для того чтобы иметь возможность реализовать целевые установки по затратам, при этом обеспечив необходимые потребительские свойства. | Реорганизация бизнес-процессов | 51 069,616 |
ИТОГО | 76 604,423 |
Основную долю в себестоимости продукции МЗХ ЗАО «Атлант» составляют материальные затраты (таблица 3.4).
Таблица 3.4 – Доля и структура материальных затрат в себестоимости продукции
Показатель | 2006 | 2007 | 2008 | |||
млн.р. | % | млн.р. | % | млн.р. | % | |
Себестоимость объема произведенной продукции, в т.ч. | 361 867 | 100 | 464 512 | 100 | 550 719 | 100 |
Материальные затраты | 273 253 | 76 | 364 621 | 78 | 422 231 | 77 |
из них: | ||||||
основные материалы, сырье | 107 997 | 40 | 123 140 | 34 | 137 379 | 33 |
покупные комплектующие, кооперация | 146 214 | 54 | 216 278 | 59 | 252 400 | 60 |
вспомогательные материалы | 11 038 | 4 | 13 841 | 4 | 19 451 | 5 |
топливо, энергия | 8 003 | 3 | 11 362 | 3 | 13 001 | 3 |
Применим систему целевого планирования к данным о производственно-хозяйственной деятельности МЗХ ЗАО «Атлант». В качестве годового объема продаж примем фактический уровень в 1 006 509 холодильников.
Целевая цена определяется уровнем установившейся рыночной цены на продукцию. Определение целевой цены должно быть возложено на руководящий состав коммерческого отдела. Исследования рынка показали, что в качестве целевой может быть принята цена на уровне 650 600 р. Норма прибыли сохраняется на прежнем уровне: 16,7 %. Рассчитаем размер целевой себестоимости по формуле 8.
Сц = (Цц
– Цц ∙ Нпр /100) N
, (8)
где Сц – целевая себестоимость, млн. р.;
Цц – целевая цена, р.;
Нпр – норма прибыли, %;
N – планируемый объем продаж, шт.
Таким образом, размер целевой себестоимости составит:
Сц = (650 600 – 650 600 ∙ 16,7/100) ∙ 1 006 509 = 545 478 млн. р.
Фактическая себестоимость продукции предприятия составила 550 719 млн. р. Отклонение фактической себестоимости от целевой: 550 719 – 545 478 = 5 241 млн. р.
Для снижения издержек предлагаю применять метод разработки максимально экономичных изделий, который условно можно разделить на три основных этапа:
Снижение количества деталей продукции. В результате проведенных маркетинговых исследований было установлено, что комплектация некоторых моделей холодильников может быть пересмотрена с целью снижения материальных затрат в части основных материалов и сырья. Предлагается пересмотреть комплектацию холодильников МХ-2822,2823 и МХ-5810,5811.
Годовой выпуск холодильников данных моделей составляет 38 170 шт. В том числе 19 285 шт. холодильников МХ-5811,2823 и 18 885 шт. холодильников МХ-5811,2822.
Расчет экономии производим по формуле 9.
,
(9)
где Цi – цена i-ого комплектующего изделия, р.;
Npi – норма расхода i-ого комплектующего изделия, шт.;
Ni – количество холодильников с данным комплектующим изделием, шт.
Данные по снижению себестоимости за счет данного мероприятия сведем в таблицу 3.5.
Таблица 3.5 – Снижение материальных затрат за счет оптимизации количества комплектующих изделий.
Наименование | Цена, р. | Норма расхода, шт. | Эффект, р. | |
до внедрения | после внедрения | |||
1 | 2 | 3 | 4 | 5 |
Бак | 1 001 | 1 | 0 | 38 208 170 |
Крышка бака | 535 | 1 | 0 | 20 420 950 |
Емкость | 279 | 2 | 0 | 21 298 860 |
Крышка | 125 | 2 | 0 | 9 542 500 |
Барьер-полка | 596 | 1 | 0 | 11 493 860 |
596 | 2 | 0 | 22 510 920 | |
Снижение себестоимости в расчете на год: | 123 475 260 |
Замена дорогостоящих компонентов более дешевыми. Одним из вариантов может стать смешивание материалов с целью уменьшения доли более дорогостоящей составляющей при условии сохранения свойств материала. Таким образом, предлагаю применять смесь из эластокула, ИЗО ПМДИ и циклопентана (таблица 3.6).
Таблица 3.6 - Снижение материальных затрат за счет оптимизации состава применяемых материалов.
Материал | Цена, р./кг | Плановая экономия, кг/год | Расчет | Экономия за год, р. |
1 | 2 | 3 | 4 | 5 |
Эластокул | 4 120 | 45 250 | (ст.3 ∙ ст.4) | 186 430 000 |
ИЗО ПМДИ | 4 519 | 69 130 | 312 398 470 | |
Циклопентан | 3 668 | 6 304 | 23 255 120 | |
Итого экономия на годовую программу | 522 083 590 |
Экономия топливно-энергетических ресурсов (таблица 3.7).
Таблица 3.7 Мероприятия по экономии энергоресурсов
Наименование мероприятий | Вид энергоресурсов |
Единица измерения |
Экономия | |
в нат. ед. | в тыс. р. | |||
1 | 2 | 3 | 4 | 5 |
Установка регуляторов тепловой энергии РТМ-02 «Струмень» на тепловых пунктах корпусов завода. | теплоэнергия | Гкал | 2 405 | 70 914 |
Установка частотного преобразователя OMRON (Р=7,5 кВт) на линии сухого гранулирования МР-90-33D «POGANI» | электроэнергия | тыс. кВт. ч | 9 | 1 362 |
Установка частотного преобразователя OMRON (Р=15 кВт) на подъемнике склада ПДО | электроэнергия | тыс. кВт. ч | 13 | 1 937 |
Замена приборов регулировки нагрева приборами ТПА KASY 5000 | электроэнергия | тыс. кВт. ч | 123 | 18 032 |
Внедрение двухместной литьевой формы на деталь «Емкость 301.54-3.1.082» | электроэнергия | тыс. кВт. ч | 71 | 10 399 |
Внедрение изготовления панелей внутренних на термоформовочных линиях ILLIG (перевод с линий «Браун») | электроэнергия | тыс. кВт. ч | 129 | 18 879 |
Изменение техпроцесса окраски панелей с исключением использования ремонтной линии | электроэнергия | тыс. кВт. ч | 128 | 18 850 |
Замена окон в галерее между корпусами 1 и 1Б. | теплоэнергия | Гкал | 106 | 3 089 |
Внедрение компрессора СКОМ140Н (снижение потребляемой мощности на 10 Вт, объем выпуска - 100 тыс. шт/год | электроэнергия | тыс. кВт. ч | 1 | 148 |
Расширение выпуска холодильников энергетической эффективностью класса «А» (уменьшение потребляемой мощности на 12 Вт, объем выпуска - 100 тыс. шт/год) | электроэнергия | тыс. кВт. ч | 1 | 176 |
Расширение выпуска холодильников на хладоне К600А (снижение потребляемой мощности на 3 Вт, объем выпуска -350 тыс. шт./год) | электроэнергия | тыс. кВт. ч | 1 | 154 |
Изменение конструкции подвески № 7878-6482-02 |
топливо |
тыс. н. м3 |
17 | 2 260 |
Автоматическое регулирование давления сжатого воздуха после 2-ой ступени в компрессоре высокого давления №12 | электроэнергия | тыс. кВт. ч | 4 | 605 |
Внедрение децентрализованной системы оборотного водоснабжения на участке экструзии в корпусе №12 | электроэнергия | тыс. кВт. ч | 160 | 23 463 |
Вывод из эксплуатации 5-ти единиц устаревшего металлорежущего оборудования и каменной электропечи, в связи с реорганизацией участка заготовок и термообработки. | электроэнергия | тыс. кВт. ч | 65 | 9 447 |
Внедрение методики ускоренных испытаний холодильников МХМ 1802,1803,1807,1809, 1816 на изобутане. | электроэнергия | тыс. кВт. ч | 1 | 116 |
Расширение выпуска холодильников класса «А» (снижение потребляемой мощности при приемо-сдаточных испытаниях) | электроэнергия | тыс. кВт. ч | 1 | 91 |
Перевод системы оборотного водоснабжения корпуса №8 с децентрализованного на локальное. | электроэнергия | тыс. кВт. ч | 53 | 7 938 |
ИТОГО ГОДОВАЯ ЭКОНОМИЯ | 187 859 |
Итого экономический эффект от внедрения мероприятий в рамках целевого планирования затрат составит 756 813,427 тыс. р.
3.1.3 Совершенствование методологии учета затрат
Для достижения цели снижения себестоимости необходимо иметь представление о реальном уровне затрат на производимую продукцию. В разделе 1.2 были рассмотрены основные методы учета и распределения затрат. На мой взгляд, наиболее отвечающим целям мониторинга уровня себестоимости и определения избыточных затрат, является Activity based costing (ABC). Данный метод имеет несколько вариантов перевода на русский язык (например, «Функционально-стоимостной анализ», «Функциональная система распределения затрат»). Однако более правильным кажется перевод метода как «Операционно-ориентированный метод калькуляции себестоимости» либо «Пооперационный метод». В данной работе будут использованы именно эти варианты перевода, как наиболее полно отражающие сущность рассматриваемого понятия.
Пооперационный метод устраняет два самых крупных недостатка традиционных методов учета:
– отсутствие ориентации на экономию затрат и реинжиниринг бизнес-процессов;
– невозможность точного подсчета полных издержек производства отдельного продукта.
Базовым принципом расчета себестоимости является разделение затрат на прямые и косвенные (накладные) и отнесение обоих видов затрат на готовую продукцию. Как правило, на практике с распределением прямых затрат проблем не возникает, поскольку они могут быть напрямую отнесены на себестоимость конкретного объекта затрат.
Косвенные расходы традиционно переносятся на объекты затрат пропорционально размеру трудозатрат, машинному времени, объему производства, продаж. Если доля косвенных расходов в себестоимости выпускаемой продукции (работ, услуг) невелика, применение традиционного подхода к себестоимости оправдывает себя ввиду его простоты и незначительной погрешности результата. Однако в современных условиях при совершенствовании технологии производства, снижении его трудоемкости и материалоемкости, а также автоматизации процессов доля прямых издержек снижается, а доля косвенных расходов (на общее управление, маркетинг, финансовое управление, управление персоналом) увеличивается. Продукты, потребляющие меньше всего ресурса, пропорционально которому распределяются косвенные расходы, при расчетах будут казаться более рентабельными по сравнению с продуктами, потребляющими больше ресурсов. Использование пооперационной методики для распределения косвенных затрат позволяет избежать этих ошибок.
Процесс расчета себестоимости производимой продукции (работ, услуг) с применением операционно-ориентированного метода предполагает калькуляцию затрат в три этапа [11, стр. 31].
На первом этапе стоимость косвенных затрат на предприятии переносится на ресурсы пропорционально выбранным драйверам затрат. На втором этапе разрабатывается структура операций, необходимых для создания продукции (работ, услуг). После этого стоимость ресурсов, рассчитанная на предыдущем этапе, переносится на операции пропорционально выбранным драйверам ресурсов. На третьем этапе стоимость операций поглощается объектами затрат пропорционально драйверам операций. Результатом этого является рассчитанная себестоимость объектов затрат, например продукции.
На основании данных о реальной себестоимости выпускаемой продукции предприятие может принимать решения об изменении товарного ассортимента, снижении цены и ликвидации канала сбыта.
Таким образом, метод АВС позволяет принимать обоснованные решения в отношении:
– снижения издержек. Реальная картина издержек дает возможность точнее определять виды затрат, которые необходимо оптимизировать;
– ценовой политики. Точное отнесение издержек на объекты калькуляции позволяет определить нижнюю границу цен, дальнейшее снижение которых относительно такой границы ведет к убыточности продукта;
– товарно-ассортиментной политики. Реальная себестоимость позволяет разработать программу действий по отношению к тому или иному продукту - снять с производства, оптимизировать издержки или поддерживать на текущем уровне;
– оценки стоимости операций. Можно решить, целесообразно ли передавать те или иные операции подрядчикам или необходимо проводить организационные преобразования.
Сегодня существует множество программных решений, поддерживающих метод АВС. Для отдела контроллинга предлагается внедрение системы «ABIS.ABC». Программная система «ABIS.ABC» позволяет создавать прикладные АВС-системы управленческого учета затрат, расчета производительности и стоимости бизнес-процессов, себестоимости продукции (услуг) и формировать аналитическую отчетность для предприятий любого масштаба и сферы деятельности.
Произведем оценку стоимости требуемого программного обеспечения (таблица 3.8).
Таблица 3.8 – Стоимость программного обеспечения
Компонент | Стоимость, р. |
1С: Предприятие 8. "1С-ВИП Анатех: ABIS.ABC. Управленческий учет и расчет себестоимости" | 4 757 760 |
1С-ВИП Анатех: ABIS.ABC. Управленческий учет и расчет себестоимости", многопользовательская лицензия на 5 рабочих мест | 15 859 200 |
ИТОГО | 20 616 960 |
Оценим бюджет и сроки внедрения системы (таблица 3.9).
Таблица 3.9- Бюджет и сроки проекта внедрения ABIS.ABC - системы
Наименование этапа проекта | Сроки | Стоимость, р. |
Предварительное обследование. Формирование команды проекта. | 10 дней | 7 756 000 |
Предварительный работы по формализации бизнес-процессов предприятия, обучение персонала | 1 мес. | 27 700 000 |
Внедрение программного обеспечения, реализующего разработанную систему и пуско-наладочные работы. | 1,5 мес. |
44 320 000 (без учета стоимости ПО и лицензий) |
ИТОГО | 79 776 000 | |
Стоимость программного обеспечения | 20 616 960 | |
ИТОГО С УЧЕТОМ СТОИМОСТИ ПО | 100 392 960 |
Использование пооперационного метода расчета себестоимости позволит оптимизировать ассортимент выпускаемой продукции за счет дифференцированного подхода к различным моделям продукции и оценить целесообразность производства отдельных комплектующих собственными силами. Предполагается, что за счет оптимизации производства произойдет снижение себестоимости выпускаемой продукции на 38 550 тыс. р. Таким образом, годовая эффективность использования пооперационного метода расчета себестоимости составит минус 61 845 960 р.
Определим срок окупаемости проекта. Капитальные вложения составят 100 392, 960 тыс. р. Годовой доход первого года составит 38 550 тыс. р. Дисконтированный доход второго года будет равен 32 670 тыс. р., третьего - 23 503 тыс.р., четвертого – 14 331 тыс. р. Таким образом, дисконтированный срок окупаемости проекта составит 3,4 года.
В результате внедрения представленных мероприятий, на предприятии сложится следующая система управления затратами (рисунок 7).
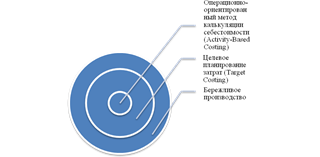
Рисунок 7 – Иерархия инструментов управления затратами
Оперативный уровень представлен операционно-ориентированным методом расчета себестоимости, стратегический - целевым планированием затрат. Данные уровни подчинены концепции «Бережливо производство». Общее управление осуществляется отделом контроллинга.
Годовой эффект от внедрения представленных мероприятий составит 3 723 313 тыс. р.
3.2 Совершенствование процесса производства печатной платы
Современная бытовая техника оснащается электронным блоком управления. Техника производства МЗХ ЗАО «Атлант» не является исключением. Новые модели снащены электронным блоком управления на основе печатных плат.
Применение печатных плат, позволяет увеличить:
– надежность элементов, узлов и техники в целом;
– технологичность, за счет автоматизации некоторых процессов сборки и монтажа;
– плотность размещения элементов за счет уменьшения габаритов и массы;
– быстродействие;
– помехозащищенность элементов и схем.
Особое значение при конструировании печатных плат имеют стандарты: ГОСТы, ОСТы, СТП. В настоящее время их используется до нескольких десятков. Одними из основных документов являются: ГОСТ 23751-86 и ГОСТ 23752-79. ГОСТ 23751-86 устанавливает основные конструктивные параметры ПП (размеры печатных проводников, зазоров, контактных площадок, отверстий и т.п.), позиционные допуски расположения элементов конструкций, электрические параметры. ГОСТ 23752-79 определяет требования к конструкции ПП и ее внешнему виду, к электрическим параметрам, к паяемости и перепайке, к устойчивости при климатических и механических воздействиях.
Печатные платы (ПП) предназначены для электрического соединения элементов схемы между собой и в общем, случае представляют вырезанный по размеру материал основания, содержащий необходимые отверстия и проводящий рисунок, который может быть выполнен как на поверхности, так и в объеме основания.
В настоящее время известно более 40 различных технологических методов изготовления печатных плат. Метод изготовления печатных плат необходимо выбирать при эскизной компоновке аппаратуры, в процессе которой определяются основные габариты и размеры плат, требуемая для данных изделий плотность монтажа.
Методы изготовления ПП разделяют на две группы: субтрактивные и аддитивные.
В субтрактивных методах (subtratio — отнимание) в качестве основания для печатного монтажа используют фольгированные диэлектрики, на которых формируется проводящий рисунок путем удаления фольги с непроводящих участков. Дополнительная химико-гальваническая металлизация монтажных отверстий привела к созданию комбинированных методов изготовления ПП. По субтрактивной технологии рисунок проводников получается травлением медной фольги по защитному изображению в фоторезисте или металлорезисте. Применяются три разновидности субтрактивной технологии.
Первый вариант – негативный процесс с использованием сухого пленочного фоторезиста (СПФ). Процесс достаточно простой, применяется при изготовлении односторонних и двухсторонних ПП. Металлизация внутренних стенок отверстий не выполняется. Заготовка – фольгированный диэлектрик. Методами фотолитографии с помощью сухого пленочного фоторезиста на поверхности фольги формируется защитная маска, представляющая собой изображение (рисунок) проводников. Затем открытые участки медной фольги подвергаются травлению, после чего фоторезист удаляется.
Второй вариант – позитивный процесс. Создается проводящий рисунок двухсторонних слоев с межслойными металлизированными переходами (отверстиями). Сухой пленочный фоторезист (СПФ) наслаивается на заготовки фольгированного диэлектрика, прошедшие операции сверления отверстий и предварительной (пять - семь мкм) металлизации медью стенок отверстий и всей поверхности фольги. В процессе фотолитографии СПФ защитный рельеф получают на местах поверхности металлизированной фольги, подлежащей последующему удалению травлением. На участки, не защищенные СПФ, последовательно осаждаются медь и металлорезист (сплав SnPb), в том числе и на поверхность стенок отверстий. После удаления маски СПФ незащищенные (более тонкие) слои меди вытравливаются. Процесс более сложный, однако, с его помощью удается получить металлизированные стенки отверстий.
Третий вариант – так называемый тентинг-процесс. Как и в позитивном процессе, берется заготовка в виде фольгированного диэлектрика, формируются отверстия, проводится предварительная металлизация всей платы, включая внутренние стенки отверстий. Затем наносится СФП, который формирует маску во время фотолитографии в виде рисунка печатных проводников и образует завески – тенты над металлизированными отверстиями, защищая их во время последующей операции травления свободных участков медной фольги. В этом процессе используются свойства пленочного фоторезиста наслаиваться на сверленые подложки без попадания в отверстия и образовывать защитные слои над металлизированными отверстиями. Применение тентинг-метода упрощает технологический процесс изготовления двусторонних ПП с металлизированными отверстиями. Однако необходимо обеспечить гарантированное запечатывание отверстий фоторезистом. Кроме того, качество поверхности металла вокруг отверстий должно быть очень хорошим, без заусениц.
Для получения изображений используется пленочный фоторезист толщиной 15-50 мкм. Толщина фоторезиста в случае метода «тентинг» диктуется требованиями целостности защитных завесок над отверстиями на операциях проявления и травления, проводимых разбрызгиванием проявляющих и травящих растворов под давлением 1,6-2 атм. и более. Фоторезисты толщиной менее 45-50 мкм на этих операциях над отверстиями разрушаются.
Подготовка поверхностей заготовок под наслаивание пленочного фоторезиста с целью удаления заусенцев сверленых отверстий и наростов гальванической меди производится механической зачисткой абразивными кругами с последующей химической обработкой в растворе персульфата аммония или механической зачисткой водной пемзовой суспензией. Такие варианты подготовки обеспечивают необходимую адгезию пленочного фоторезиста к медной поверхности подложки и химическую стойкость защитных изображений на операциях проявления и травления. Кроме того, механическая зачистка пемзой дает матовую однородную поверхность с низким отражением света, обеспечивающая более однородное экспонирование фоторезиста.
Фоторезист наслаивается по специально подобранному режиму: при низкой скорости наслаивания 0,5 м/мин, при температуре нагрева валков 115 °С ± 5 °С, на подогретые до температуры 60 ÷ 80 °С заготовки. При экспонировании изображения используются установки с точечным источником света, обеспечивающим высококоллимированный интенсивный световой поток на рабочую поверхность с автоматическим дозированием и контролем световой энергии.
Субтрактивный метод получения рисунка проводников ПП основан на травлении медной фольги по защитной маске. Из-за процессов бокового подтравливания меди под краями маски поперечное сечение проводников имеет форму трапеции, расположенной большим основанием на поверхности диэлектрика. Величина бокового подтравливания и, соответственно, разброс ширины создаваемых проводящих дорожек зависит от толщины слоя металла: при травлении фольги толщиной пять мкм интервал разброса ширины проводников порядка семь мкм, при травлении фольги толщиной 20 мкм разброс составляет 30 мкм, а при травлении фольги толщиной 35 мкм разброс составляет около 50 мкм.
Искажения ширины медных проводников по отношению к размерам ширины их изображений в фоторезисте и на фотошаблоне смещаются в сторону заужения. Следовательно, при субтрактивной технологии размеры проводников на фотошаблоне необходимо увеличивать на величину заужения. Из этого следует, что субтрактивная технология имеет ограничения по разрешению, которые определяются толщиной фольги и процессами травления. Минимально воспроизводимая ширина проводников и зазоров составляет порядка:
– 50 мкм при толщине фольги пять - девять мкм;
– 100 - 125 мкм при толщине проводников 20 - 35 мкм;
– 150 - 200 мкм при толщине проводников 50 мкм.
Аддитивные (additio - прибавление) методы основаны на избирательном осаждении токопроводящего покрытия на диэлектрическое основание, на которое предварительно может наноситься слой клеевой композиции. Применение аддитивного метода в массовом производстве ПП ограничено низкой производительностью процесса химической металлизации, интенсивным воздействием электролитов на диэлектрик, трудностью получения металлических покрытий с хорошей адгезией. Доминирующей в этих условиях является субтрактивная технология, особенно с переходом на фольгированные диэлектрики с тонкомерной фольгой (пять и 18 мкм).
Для изготовления печатных плат с шириной проводников и зазоров 50 -100 мкм с толщиной проводников 30-50 мкм рекомендуется использовать аддитивный метод формирования рисунка (метод ПАФОС). Это полностью аддитивный электрохимический метод, по которому проводники и изоляция между ними (диэлектрик) формируются селективным гальваническим осаждением проводников и формированием изоляции только в необходимых местах прессованием. Метод ПАФОС, как аддитивный метод, принципиально отличается от субтрактивного тем, что металл проводников наносится, а не вытравливается. Проводящий рисунок формируется последовательным наращиванием слоев:
– получение на временных "носителях" - листах из нержавеющей стали - медной шины толщиной 2÷20 мкм;
– формирование рисунка в СПФ;
– гальваническое осаждение тонкого слоя никеля (два ÷ три мкм) и меди (30 ÷ 50 мкм) по рисунку освобождений в рельефе пленочного фоторезиста. В защитном рельефе пленочного фоторезиста на верхнюю поверхность сформированных проводников производится также нанесение адгезионных слоев.
После этого пленочный фоторезист удаляется, и проводящий рисунок на всю толщину впрессовывается в диэлектрик. Полученный прессованный слой вместе с медной шиной механически отделяется от поверхности носителей.
При изготовлении двухсторонних слоев с межслойными переходами перед травлением тонкой медной шины сверлятся и металлизируются отверстия. Проводящий рисунок, утопленный в диэлектрик и сверху защищенный слоем никеля, при травлении медной шины не подвергается воздействию травильного раствора. Поэтому форма, размеры и точность проводящего рисунка определяются формой и размерами освобождений в рельефе пленочного фоторезиста, т.е. процессами фотохимии (фотолитографии). Отсюда к процессам фотолитографии предъявляются более жесткие требования, в частности, оптической плотности белых и черных полей фотошаблонов, резкости края изображения, стабильности температуры и влажности в рабочих помещениях.
Профиль фоторельефа пленочного фоторезиста зависит от применяемой модели светокопировальной установки. При экспонировании на установках с совершенной экспонирующей системой, обеспечивающей высокую коллимацию высокоинтенсивных световых лучей и отсутствие нагрева рабочей копировальной поверхности, фоторельеф имеет ровные боковые стенки с малым наклоном к поверхности подложки.
Методы нанесения рисунка ПП. Основными методами, применяемыми в промышленности для создания рисунка печатного монтажа, являются офсетная печать, сеткография и фотопечать. Выбор метода определяется конструкцией ПП, требуемой точностью и плотностью монтажа, производительностью оборудования и экономичностью процесса.
Метод офсетной печати состоит в изготовлении печатной формы, на поверхности которой формируется рисунок слоя. Форма закатывается валиком трафаретной краской, а затем офсетный цилиндр переносит краску с формы на подготовленную поверхность основания ПП.
Метод применим в условиях массового и крупносерийного производства с минимальной шириной проводников и зазоров между ними 0,3-0,5 мм (платы первого и второго классов плотности монтажа) и с точностью воспроизведения изображения ±0,2 мм. Его недостатками являются высокая стоимость оборудования, необходимость использования квалифицированного обслуживающего персонала и трудность изменения рисунка платы.
Сеткографический метод основан на нанесении специальной краски на плату путем продавливания ее резиновой лопаткой (ракелем) через сетчатый трафарет, на котором необходимый рисунок образован ячейками сетки, открытыми для продавливания. Метод обеспечивает высокую производительность и экономичен в условиях массового производства. Точность и плотность монтажа аналогичны предыдущему методу.
Самой высокой точностью (±0,05 мм) и плотностью монтажа, соответствующими третьему — пятому классу (ширина проводников и зазоров между ними 0,1- 0,25 мм), характеризуется метод фотопечати. Он состоит в контактном копировании рисунка печатного монтажа с фотошаблона на основание, покрытое светочувствительным слоем (фоторезистом).
Однослойные ПП и ГПК изготавливают преимущественно субтрактивным сеточно-химическим или аддитивным методом, а ДПП и ГПП химико-гальваническим аддитивным или комбинированными фотохимическими (негативным или позитивным) методами. Производство МПП основано на типовых операциях получения ОПП и ДПП и некоторых специфических процессах, таких как прессование слоев, создание межслойных соединений и др.
Выбор метода изготовления МПП определяется следующими факторами: числом слоев, надежностью соединений, плотностью монтажа, видом выводов устанавливаемых ЭРЭ и ИС, возможностью механизации и автоматизации, длительностью производственного цикла, экономичностью. Методы, основанные на использовании объемных деталей для межслойных соединений, характеризуются повышенной трудоемкостью, низкой надежностью, плохо поддаются автоматизации. Наиболее распространен из второй группы метод металлизации сквозных отверстий.
Конструкционные материалы печатных плат. Для изготовления ПП широкое распространение получили слоистые диэлектрики, состоящие из наполнителя и связующего вещества (синтетической смолы, которая может быть термоактивной или термопластичной), керамические и металлические (с поверхностным диэлектрическим слоем) материалы.
Выбор материала определяется электроизоляционными свойствами, механической прочностью, обрабатываемостью, стабильностью параметров при воздействии агрессивных сред и изменяющихся климатических условий, себестоимостью. Ниже в таблице 3.10 представлены материалы основания ПП, наиболее часто используемые в настоящее время для изготовления ОПП, ДПП.
Таблица 3.10 Материалы основания ПП для изготовления ОПП, ДПП
Материал | Марка |
Толщина, мм |
Материал | Марка |
Толщина, мм |
1 | 2 | 3 | 4 | 5 | 6 |
Гетинакс фольгированный | ГФ-1-35 |
1,0; 1,5; 2,0; 2,5; 3,0 |
Диэлектрик фольгированный общего назначения с гальваностойкой фольгой |
ДФО-1, ДФО-2 (фольга 35 мкм) ДФС-1, ДФС-2 (фольга 20 мкм) |
0,06-2,0 |
Гетинакс фольгированный с гальваностойкой фольгой |
ГФ-1-35Г ГФ-2-35Г ГФ-1-50Г ГФ-2-50Г |
Диэлектрик фольгированный самозатухающий с гальваностойкой фольгой | |||
Стеклотекстолит фольгированный |
СФ-1-35 СФ-2-35 СФ-1-50 СФ-2-50 |
0,5; 1,0; 1,5; 2,0; 2,5; 3,0 |
Стеклотекстолит фольгированный с повышенной на-гревостойкостью |
СФПН-1-50 СФПН-2-50 |
0,5; 1,0; 1,5; 2,0; 2,5; 3,0 |
То же с гальваностойкой фольгой | Стеклотекстолит фольгированный общего назначения |
СОНФ-1 СОНФ-2 |
— | ||
Стеклотекстолит теплостойкий фольгированный с гальваностойкой фольгой | СТФ-1-35 СТФ-2-35 СТФ-1-18 СТФ-2-18 |
0,08; 0,1; 0,13; 0,2; 0,15; 0,3; 0,25; 0,5; 0,35; 0,8; 1,5; 2,5; 1; 2;3 |
Гетинакс фольгированный общего назначения |
ГОФ-1-35Г ГОФ-2-35Г |
— |
Стеклотекстолит с двусторонним адгезионным слоем | СТЭК | 1,0; 1,5 | |||
Стеклотекстолит теплостойкий и негорючий фольгированный с гальваностойкой фольгой | СТНФ-1-35 СТНФ-2-35 СТНФ-1-18 СТНФ-2-18 | Стеклотекстолит теплостойкий, армированный алюминиевым протектором |
СТПА-5-1 СТПА-5-2 (фольга 5 мкм) |
0,1-2,0 | |
Стеклотекстолит листовой | СТЭФ-1-2ЛК | 1;2 | Стеклотекстолит с катализатором | СТАМ | 0,7-2,0 |
Стеклотекстолит электротехнический | СТЭФ-ВК-1-1,5 | Фольгированный армированный фторопласт |
ФАФ-4 (фольга 35 мкм) |
— | |
Стеклотестолит фольгированный теплостойкий | СТФТ | — | Стеклотекстолит теплостойкий | СТАЛ (фольга 5, 18, 35, 50, 70 и 100 мкм на медном или алюминиевом протекторе) | — |
По сравнению с гетинаксами стеклотекстолиты имеют лучшие механические и электрические характеристики, более высокую нагревостойкость, меньшее влагопоглощение. Однако у них есть ряд недостатков: худшая механическая обрабатываемость; более высокая стоимость; существенное различие (примерно в 10 раз) коэффициента теплового расширения меди и стеклотекстолита в направлении толщины материала, что может привести к разрыву металлизации в отверстиях при пайке или в процессе эксплуатации.
Соединение отдельных слоев МПП осуществляют специальными склеивающими прокладками, которые изготавливают из стеклоткани, пропитанной недополимеризованной эпоксидной смолой. Содержание смолы в прокладках должно быть в пределах 42-52%, а летучих веществ не более 0,75 %. Длительное сохранение клеящих свойств межслойных прокладок достигается их консервацией в герметически упакованных полиэтиленовых мешках при пониженной (+10°С) температуре.
Изготовление фотошаблонов. Изображение рисунка проводников ПП, разработанное на стадии создания конструкторской документации на изделие, должно быть перенесено на защитную маску фото- или металлорезиста в зависимости от типа применяемого процесса для создания ПП. Для переноса изображения предназначены фотошаблоны (ФШ), представляющие собой негативное или позитивное отображение конфигурации печатных проводников, выполненное в натуральную величину на светопроницаемом основании. Комплектом фотошаблонов называют то количество фотошаблонов, совмещающихся между собой, которое необходимо и достаточно для изготовления ПП определенного типа и наименования. По назначению они разделяются на контрольные (эталоны), и рабочие, которые изготавливаются с контрольных методом контактной печати и служат для перенесения имеющегося на них рисунка на плату.
Изображение элементов на фотошаблоне должно соответствовать требованиям чертежа и быть черно-белым, контрастным с четкими и ровными границами при оптической плотности темных полей не менее 2,5-3 ед. и прозрачных участков не более 0,15-0,2 ед., замеренной с точностью ±0,02 ед. на фотоэлектрическом денситометре типа. Размеры печатных проводников и контактных площадок устанавливаются с учетом величины подтравливания. Фотошаблон должен быть износостойким, иметь минимальную деформацию при изменении температуры и влажности окружающей среды. В большей степени перечисленным требованиям удовлетворяют сверхконтрастные фотопластинки и полированные силикатные стекла с металлизированными поверхностями, на которых получают контрольные фотошаблоны. Рабочие фотошаблоны изготавливают на малоусадочных (не более 0,01-0,03%) фотопленках.
На фотошаблоны наносят также технологические контрольные знаки. Контрольный знак - специальный топологический элемент в виде штриха, щели, креста и пр., служащий для контроля точности изготовления оригиналов и фотошаблонов и применяемый для совмещения фотошаблонов слоев двусторонних и многослойных ПП, а также при выполнении операции мультипликации.
Обычно фотошаблоны получают на основе оригинала ПП, выполненного также на материале, который имеет стабильные размеры (органическое или силикатное стекло, алюминий, лавсан и др.), но в увеличенном масштабе 2:1, 4:1, 10:1. Оптимальный масштаб выбирается исходя из габаритов ПП, требуемой точности получения фотошаблона и погрешности изготовления оригинала выбранным методом:
M = dор / dфш , (11)
где dор, dфш - половина поля допуска на изготовление оригинала и фотошаблона.
Основными методами получения оригиналов являются вычерчивание, наклеивание липкой ленты и вырезание эмали.
Вычерчивание изображения оригинала на специальной бумаге или малоусадочной пленке, на которую предварительно наносится непроявляющейся синей краской с шагом 2,5±0,05 мм координатная сетка, осуществляют вручную (в основном, для макетных работ) или на автоматическом чертежном аппарате, управляемом координатографом.
Метод аппликаций состоит в наклеивании на прозрачное основание калиброванных одиночных и групповых элементов, изготовленных из светонепроницаемой безусадочной антистатической пленки. Для получения изображения ДПП на одну сторону основания наклеивают красные (желтые) элементы, а на другую синие (фиолетовые). Последующее фотографирование через соответствующий светофильтр обеспечивает получение совмещенного оригинала рисунков с точностью ±0,2 мм. Метод рекомендуется для изготовления ОПП и ДПП, простых по конструкции, с пониженной плотностью монтажа.
Наибольшую точность изготовления оригиналов ПП (±0,05мм) обеспечивает метод вырезания эмали. Для этого на прозрачное основание наносят равномерный слой гравировальной черной эмали, которую после сушки вырезают с пробельных мест на универсально-расточных станках, снабженных измерительными микроскопами, или на координатографах. В качестве инструмента используются пунктирные иглы, граверные резцы, рейсфедеры с алмазными наконечниками.
Из готового оригинала контрольные фотошаблоны получают масштабным фотографированием на фоторепродуционных полиграфических камерах с объективами, имеющими высокую разрешающую способность. Рабочие фотошаблоны изготавливают с контрольных способом контактной печати. Если ТП предусматривает обработку групповой заготовки (при размерах ПП до 100 мм), то на специальном оборудовании (фотоштампах) методом мультипликации получают групповой фотошаблон с точным расположением рисунков рядами и строками, общими элементами совмещения и общим машинным нулем отсчета координат программного сверления отверстий. После экспонирования и мультиплицирования осуществляется химико-фотографическая обработка фотоматериала, контроль полученного фотошаблона, ретуширование - удаление дефектов.
Более прогрессивным является метод получения фотошаблонов сканирующим световым лучом. Он выполняется на лазерных растровых генераторах изображений (фотоплоттерах) сканированием лазерного пятна по поверхности пленок или стеклянных пластин и испарением маскирующего покрытия или засветки фотоматериала в соответствии с рисунком ПП. В фотоплоттере имеется библиотека часто повторяющихся в топологических чертежах элементов и узлов.
При изготовлении крупноформатных шаблонов ПП на стеклах с маскирующим покрытием методом лазерного гравирования погрешность взаимного расположения рисунка составляет ±0,01 мм, точность позиционирования ±0,005 мм, точность повторного позиционирования ±0,002 мм, неровность края изображения ±0,01 мм, погрешность воспроизведения размеров элементов изображения ±0,015 мм, погрешность расположения элементов относительно базового отверстия ±0,015 мм.
Формирование растрового изображения рисунка (оригинала) в фотоплоттере вне зависимости от сложности рисунка происходит с высокой скоростью в течение нескольких минут. Тиражирование фотошаблонов проводится без использования методов контактной печати с высокой точностью. Работа фотоплоттеров поддерживается входными и выходными форматами систем автоматического проектирования. Это позволяет:
– получать фотошаблоны и программы сверления с цифрового планшета;
– просматривать и редактировать ФШ и программы сверления;
– создавать групповые заготовки на основе контура ПП одновременно для всех слоев;
– автоматически генерировать по ФШ программы сверления;
– подсчитывать площадь металлизации, число контактных площадок проводников, отверстий, длину проводников и пр.
Время изготовления ФШ, например, размером 550 на 550 мм с минимальной толщиной линии 0,15 мм и неровностью края экспонируемого элемента ±10 мкм составляет пять - шесть мин.
Сетчатые трафареты представляют собой металлическую раму из алюминиевого сплава, на которую натянут тканый материал. К материалу ткани предъявляются следующие требования: величина просветов должна быть в полтора — два раза больше толщины нитей; на ткани не должно быть дефектов; она должна быть прочной на разрыв, устойчивой к истиранию, эластичной и практически не должна растягиваться в процессе работы, ячейки ткани не должны взаимодействовать с растворителями краски. Наибольшей точностью и долговечностью обладают металлические сетки из нержавеющей стали или фосфористой бронзы с размером ячеек 40-50 мкм, а наиболее эластичны сетки из капрона, лавсана, металлизированного нейлонового моноволокна. Для изготовления сетчатого трафарета на поверхность рамы наносят специальный клей и укладывают сетку. Сетка равномерно натягивается таким образом, чтобы относительная деформация материала не превышала шесть-восемь процентов для капрона, пять-семь процентов для фосфористой бронзы и два – три процента для нержавеющей стали. Сетка приклеивается к раме и обезжиривается. Рисунок платы на поверхности сетки получают прямым копированием через фотошаблон нанесенной фотополимерной композиции.
Печатные формы. Конструктивно формы для офсетной печати разделяются на три вида: высокой печати, глубокой печати и с расположением печатных участков в одной плоскости. Изготавливают их из алюминия, цинка, сплавов на их основе и пластмасс с помощью травления, гравирования, прессования, обработки гидрофобизирующей жидкостью, сборки из отдельных элементов и др. Наиболее технологичной, точной и надежной оказалась печатная форма для сухого офсета. Она представляет собой пластину из алюминия толщиной 0,5-1 мм, на которую наносится тонкая пленка силиконового лака, не смачиваемого трафаретной краской. На пленке при помощи лазерного гравировального автомата выжигается рисунок ПП.
4 ВЛИЯНИЕ ЭКОЛОГИЧЕСКИХ И ПРОИЗВОДСТВЕННЫХ ФАКТОРОВ УСЛОВИЙ ТРУДА НА СЕБЕСТОИМОСТЬ ПРОДУКЦИИ МЗХ ЗАО «АТЛАНТ» И МЕРОПРИЯТИЯ ПО ИХ УЛУЧШЕНИЮ
4.1 Экологическая оценка предприятия
На МЗХ ЗАО «Атлант» регулярно разрабатываются и реализуются мероприятия улучшению условий труда. Обеспечение безопасности и хороших условий труда требует от предприятия соответствующих целевых материальных затрат, которые находят свое отражение в себестоимости готовой продукции. Средства, израсходованные на мероприятия по совершенствованию экологической безопасности труда в 2008 году, составили 1 251 880 тыс. р.
При расчете себестоимости продукции по элементам затрат расходы по обеспечению безопасности и нормальных условий труда относят к Прочим расходам.
На предприятии в настоящее время функционируют системы оборотного водоснабжения, расположенные на промплощадке №1 и промплощадке №2.
Оборотная система водоснабжения промплощадки №1 работает следующим образом:
Отепленный хладоноситель собирается в емкость и насосом подается на брызгательный бассейн. Охлажденная в бассейне вода насосом подается на охлаждение технологического оборудования.
Системы водопровода технической воды на промплощадке №1 нет.
На промплощадке №2 имеется ввод технического водопровода из городской сети со стороны ул. Саперов. Ввод оборудован водомером MZ-150 и тремя песчаными фильтрами. Техническая вода подается в цеха предприятия за счет давления в городской сети. При понижении давления воды в городской сети, на предприятии имеется запасно-регулирующая емкость, объемом 630 куб. метров.
Оборотная система водоснабжения промплощадки №2 предназначена только для охлаждения оборудования, расположенного в корпусе №25. Компрессоры, холодильные машины и теплообменники охлаждаются за счет функционирования градирни.
В настоящее время на предприятии принята политика обустройства локальных схем оборотных систем водоснабжения, что повышает надежность работы оборудования, снижает потребление электроэнергии. Участок экструзии листа, в корпусе №12, работает вне общезаводской оборотной системы водоснабжения. В 2008 году на локальную систему переведен корпус №8. В 2009 году будет закончено проектирование перевода корпуса №4.
На предприятии имеются следующие очистные сооружения:
– очистные сооружения гальваники;
– очистные сооружения окраски (корпус №1);
– очистные сооружения окраски (корпус №12);
– очистные сооружения мойки автотранспорта;
– очистные сооружения оборотной системы водоснабжения участка экструзии;
– очистные сооружения промдождевых вод.
Характеристика очистных сооружений Минского завода холодильников приведена в приложении В. Как видно из данного приложения, отдельные очистные сооружения предприятия, в частности очистные сооружения гальваники и окраски (корпус 12), имеют фактическую загрузку ниже проектного уровня. А то же время, имеет место превышение сбросов загрязняющих веществ, таких как железо (на 21 мг/л) и цинк (на 0,9 мг/л).
4.2 Пути улучшения экологических условий труда
На МЗХ ЗАО «Атлант» регулярно разрабатываются и реализуются мероприятия по охране труда, улучшению условий труда и техники безопасности. Обеспечение безопасности и хороших условий труда требует от предприятия соответствующих целевых материальных затрат, которые находят свое отражение в себестоимости готовой продукции. Средства, израсходованные на мероприятия по охране труда в 2008 году, составили 856,9 млн. р.
При расчете себестоимости продукции по элементам затрат расходы по обеспечению безопасности и нормальных условий труда относят к Прочим расходам. В пункт «Расходы на охрану труда» включаются следующие элементы:
– стоимость материалов, топлива, энергии на содержание, эксплуатацию, текущий ремонт зданий, сооружений, инвентаря, приборов, ведение технологических процессов для охраны окружающей среды;
– оплата труда и расходы, связанные с использованием труда персонала, занятого обеспечением безопасности труда и охраной окружающей среды в обособленных структурных подразделениях;
– амортизация зданий, сооружений, оборудования, используемых в структурных подразделениях для обеспечения безопасности труда (в части, относящейся к данной статье затрат);
– износ малоценных, быстроизнашивающихся предметов, инвентаря, приборов, используемых для обеспечения безопасности труда;
– платежи за выбросы (сбросы) загрязняющих веществ в части, относимой на себестоимость продукции;
– другие затраты, осуществляемые для обеспечения безопасности труда и охраны окружающей среды.
Большое значение улучшения условий труда объясняется тем, что они в основном представляют собой производственную среду, в которой протекает жизнедеятельность человека во время труда. От их состояния в прямой зависимости находится уровень работоспособности человека, результаты его работы, состояние здоровья, отношение к труду. Улучшение условий труда существенно влияет на повышение его производительности. В связи с этим, как показывает практика, затраты на их осуществление окупаются в среднем за 3 – 5 лет. Вообще факторы, формирующие условия труда, делятся на две большие группы: факторы, не зависящие от особенностей производства, и факторы, определяемые особенностями производства. К первой группе относятся естественно-природные, социально-экономические и другие факторы. Факторы, относящиеся ко второй группе, подразделяются на производственные и социально-психологические.
Производственные факторы – это наиболее обширная группа факторов, порождаемых особенностями данного производства и формирующих специфические условия труда. Среди них выделяется несколько подгрупп: психофизиологические, санитарно-гигиенические, эстетические, хозяйственно-бытовые, организационные, материальные.
За 2008 г. на МЗХ зарегистрировано семь несчастных случаев на производстве.
Причины:
– нарушение требований безопасности труда другим работником;
– неудовлетворительная организация производства ремонтных работ;
– привлечение потерпевшей к работе не по специальности;
– невнимательность потерпевшего;
– отсутствие технологического процесса на ремонтные работы;
– допуск потерпевшего к работе без обучения;
– неудовлетворительная организация рабочих мест;
– нарушение техпроцесса.
Снижение себестоимости путем уменьшения расходов на охрану труда является сложнейшей задачей, потому что улучшение условий труда требует прямых финансовых вложений. Снижение затрат в части обеспечения оптимальных условий работы, может поставить под угрозу жизнь и здоровье работающих. Администрацией предприятия ведется работа по предупреждению несчастных случаев и заболеваемости на производстве, обеспечению безопасных и здоровых условий труда и производственного быта, исключению тяжелых физических работ.
На предприятии внедрена система контроля над состоянием охраны труда и техники безопасности в структурных подразделениях, которой предусмотрены регулярные проверки. По всем проведенным проверкам и обследованиям выдаются предписания и издаются приказы с разработкой мероприятий по устранению выявленных нарушений.
Все работающие обеспечены спецодеждой, спецобувью и другими средствами индивидуальной защиты в соответствии с нормами бесплатной выдачи средств индивидуальной защиты, установленными Министерством труда и социальной защиты. Функционирует пункт стирки и подгонки спецодежды.
Для обеспечения безопасных условий труда рабочих предусмотрены следующие меры:
– расстановка оборудования соответствует точности технологического процесса и действующим технологическим нормам;
– на всех движущихся и вращающихся частях и механизмах предусмотрены ограждения и предупреждающая окраска;
– налажена четкая система инструктажа по технике безопасности;
– предусмотрены ремонтные площадки и подъемно-транспортные механизмы;
– проводятся работы по сокращению и ликвидации тяжелых физических работ и уменьшению численности работающих, занятых ручным трудом.
Для обеспечения благоприятных условий труда работающих большое значение имеют вопросы санитарного благоустройства предприятия и организации, санитарно-бытового обслуживания рабочих.
Производственные помещения должны быть светлыми, теплыми и сухими. Площади рабочих помещений должны быть такими, чтобы на одного рабочего приходилось не менее четырех квадратных метров. Объем производственного помещения для одного работающего должен составлять не менее 15 м3. Окна должны быть оборудованы открывающимися форточками или фрамугами независимо от вентиляционных сооружений. Световые фонари застекляются армированным стеклом. Если для этой цели применяют простое стекло, то под фонарями подвешивают металлические сетки.
Температура воздуха в производственных помещениях в холодный и переходный период определяется характеристикой производственного помещения и категорией работы. Учитывая, что на МЗХ ЗАО «Атлант» основная часть работ относится к категории средней и легкой, температура в помещении в холодное время года должна быть не ниже 18-21 оС при относительной влажности 60-40% и скорости воздуха до 0,2 м/с; при выполнении тяжелых работ температура в помещении должна быть не ниже 16-18 оС при относительной влажности 60-40% и скорости воздуха 0,3 м/с. Производственные помещения должны быть снабжены доброкачественной питьевой водой температурой не выше +20 и не ниже +8 оС на расстоянии не более 75 м от рабочих мест. Расстояние от цеха до туалетного помещения не должно превышать 100 м.
Зоны с повышенным уровнем звука должны быть обеспечены знаками безопасности.
Для обеспечения необходимого микроклимата на рабочих местах в помещениях оборудуют вентиляцию и отопление. Устройство вентиляции является обязательным. Может использоваться естественная, механическая и смешанная вентиляция, обеспечивающая воздухообмен 20 м3/ч на одного человека. Местные отсосы должны обеспечивать воздухообмен 250 м3/ч.
В установленные правилами технической эксплуатации сроки должны проводиться профилактический осмотр и предупредительный ремонт вентиляционных устройств.
Для отопления производственных помещений обычно используют централизованное отопление: центральное водяное с металлическими радиаторами, лучистое с бетонными панелями. Для уменьшения потерь тепла грузовые и транспортные проемы утепляют, двери снабжают устройствами принудительного закрывания, а фрамуги, переплеты окон и световых фонарей, двери и тамбуры постоянно поддерживают в исправном состоянии.
Для обеспечения нормативных параметров микроклимата в производственных помещениях проводятся технологические, технические, санитарно-технические и организационные мероприятия.
Наиболее радикальными методами управления микроклиматом являются:
Максимально возможная механизация и автоматизация тяжелых и трудоемких работ, выполнение которых сопровождается избыточным теплообразованием в организме человека.
Дистанционное управление теплоизлучающими поверхностями, исключающее необходимость пребывания работающих в зоне инфракрасного облучения.
Рациональное размещение и теплоизоляция оборудования, коммуникаций и других источников, излучающих теплоту в рабочую зону, так, чтобы исключалась возможность совмещения потоков лучистой энергии на рабочих местах. При возможности оборудование следует размещать на открытых площадках. Теплоизоляция его должна обеспечивать температуру наружных стенок не выше 45 оС.
Оборудование источников интенсивного влаговыделения с открытой поверхностью испарения (ванны, красильные и промывочные аппараты и другие емкости с водой или растворами) крышками или снабжение их местными отсосами.
Основной способ борьбы с лучистой теплотой (инфракрасным излучением) на рабочих местах заключается в изоляции излучающих поверхностей, т.е. создании определенного термического сопротивления на пути теплового потока в виде экранов различных конструкций (жестких глухих, сетчатых полупрозрачных, водяных, водно-воздушных). Действие защитных экранов заключается либо в отражении лучистой энергии обратно к источнику излучения, либо в ее поглощении. По принципу работы различают отражающие, поглощающие, и теплоотводящие экраны. В зависимости от возможности наблюдения за ходом технологического процесса экраны можно разделить на три типа: непрозрачные, полупрозрачные и прозрачные.
Среди организационных мероприятий следует отметить следующие:
– Организация рационального водно-солевого режима работающего с целью профилактики перегрева организма. Для этого к питьевой воде добавляют небольшое количество (0,2 – 0,5%) поваренной соли и насыщают ее диоксидом углерода (сатурируют). Прием газированной подсоленной воды позволяет быстро восстанавливать нарушенное водно-солевое равновесие организма, утолять жажду, компенсировать потоотделение и соответственно снижать потери массы. Диоксид углерода придает вкус воде и улучшает секрецию желудочного сока.
– Устройство в «горячих цехах» специально оборудованных комнат, кабин или мест для кратковременного отдыха, в которые подается очищенный и умеренно охлажденный воздух.
– Для предупреждения переохлаждения и простудных заболеваний работающих у входа в цех устраивают тамбуры или создают воздушные завесы, которые направляют поток холодного наружного воздуха в верхнюю зону помещения. Для работающих длительное время на холоде предусматривают специально оборудованные помещения для обогрева.
Для обеспечения нормативных микроклиматических условий в холодный период года производственные и административно-бытовые помещения должны оборудоваться системами отопления.
Отопление проектируется для обеспечения в помещениях расчетной температуры воздуха, которая принимается в зависимости от периода года. Для холодного периода года расчет отопления производится с учетом обеспечения минимальной из допустимых температур. В общественных, административно-бытовых и производственных помещениях отапливаемых зданий, когда они не используются, и в нерабочее время следует принимать температуру воздуха ниже нормируемой, но не ниже +5оС, обеспечивая восстановление нормируемой температуры к началу использования помещения или к началу работы без увеличения приведенных затрат.
На постоянных рабочих местах в помещениях пультов управления технологическими процессами необходимо принимать расчетную температуру воздуха +22 оС и относительную влажность не более 60% в течение всего года.
Наиболее современным способом обеспечения оптимальных параметров микроклимата в помещениях является кондиционирование воздуха.
Кондиционирование воздуха – автоматическое поддержание в закрытых помещениях всех или отдельных параметров воздуха (температуры, относительной влажности, чистоты, скорости движения) с целью обеспечения, главным образом, оптимальных метеорологических условий, наиболее благоприятных для самочувствия людей, ведения технологического процесса, сохранения ценностей культуры.
В общем случае под кондиционированием понимается нагревание или охлаждение, увлажнение или осушка воздуха и очистка его от пыли. Используются различные типы кондиционеров, которые в зависимости от расхода воздуха подразделяются на промышленные, полупромышленные и бытовые.
При низком качестве кондиционеров и несовершенной технологии их обслуживания в рабочих секциях возможно накопление микроорганизмов, в том числе и патогенных. Поэтому в современных кондиционерах предусмотрена реализация дополнительных операций – обеззараживания, дезодорации, ароматизации, ионизации воздуха.
Различают системы комфортного кондиционирования, обеспечивающие в помещении постоянные комфортные условия для человека, и системы технологического кондиционирования, предназначенные для поддержания в производственном помещении требуемых технологическим процессом условий.
Аэроионы повышают умственную и физическую работоспособность, снимают стресс, укрепляют нервную систему, повышают сопротивляемость организма инфекционным заболеваниям.
Аэроионы характеризуются зарядом частиц и их подвижностью. Различают отрицательные и положительные аэроионы.
Санитарные правила регламентируют в воздушной среде помещений производственных и общественных зданий уровни аэроионизации и содержания положительных и отрицательных аэроионов (таблица 4.1).
Таблица 4.1 - Уровни аэроионизации воздушной среды производственных и общественных помещений
Уровень аэроионизации |
Число ионов в 1 см3 воздуха |
|
n+ |
n- |
|
Минимально необходимый | 400 | 600 |
Оптимальный | 1 500 – 3 000 | 3 000 – 5 000 |
Максимально допустимый | 500 | 50 000 |
Минимально необходимый и максимально допустимый уровни определяют регламентированный интервал содержания аэроионов в воздухе помещений.
Для постоянных рабочих мест в общественных помещениях при наличии источников аэроионизации принимаются оптимальные значения, а для непостоянных рабочих мест и в производственных условиях концентрация аэроионов должна находится в интервале от минимально необходимого до максимально допустимого уровней.
Технические средства ионизации или коррекции аэроионного режима помещения должны применяться в случаях, если условия пребывания персонала не удовлетворяют вышеуказанным требованиям.
Для нормализации аэроионного состава воздуха в помещениях используют приточно-вытяжную вентиляцию, групповые и индивидуальные ионизаторы воздуха, устройства автоматического регулирования ионного режима воздушной среды.
При текущем санитарном надзоре измерения содержания аэроионов производится не реже одного раза в год.
Источниками шума и вибрации являются различные процессы, оборудование, явления, что создает определенные трудности в борьбе с ними и обычно требует одновременного проведения комплекса мероприятий как инженерно-технического, так и санитарно-гигиенического характера.
Шум – совокупность звуков разной интенсивности и высоты, беспорядочно изменяющихся во времени и вызывающих у работающих неприятные субъективные ощущения. С физиологической точки зрения, шумом является любой нежелательный звук, мешающий восприятию полезных звуков в виде производственных сигналов и речи.
Шум как физический фактор представляет собой волнообразно распространяющееся механическое колебательное движение упругой среды (воздуха), носящее, как правило, беспорядочный случайный характер. При этом источником его является любое колеблющееся тело, выведенное из устойчивого состояния внешней силой.
Снижения шума и вибрации в производственных условиях можно добиться следующими методами:
– устранение или уменьшение шума и вибрации непосредственно в источнике их возникновения;
– локализация источников шума и вибрации средствами звуко- и виброизоляции; звуко - и вибропоглощения;
– рациональное размещение технологического оборудования, машин, механизмов;
– акустическая обработка помещений (снижение плотности звуковой энергии в помещении, отражений от стен, перекрытий, оборудования);
– внедрение малошумных технологических процессов и оборудования, оснащение машин и механизмов дистанционным управлением, создание рационального режима труда и отдыха работающим;
– применение средств индивидуальной защиты;
– использование лечебно-профилактических мероприятий.
Как показывает практика, наиболее эффективным является борьба с шумом в источнике его возникновения. Как правило, шум машин и механизмов возникает в результате упругих колебаний, как всего механизма, так и его частей, отдельных деталей.
Для уменьшения механического шума следует своевременно производить ремонт оборудования, шире применять принудительное смазывание трущихся поверхностей и балансировку вращающихся частей.
Действенным методом снижения уровня шума является установка звукоизолирующих и звукопоглощающих преград на пути его распространения.
При невозможности или неэкономичности реализации противошумных мероприятий, а также для работы в аварийных условиях работающие должны быть обеспечены средствами индивидуальной защиты от шума. Эффективность этих средств зависит от их конструкции, качества используемых материалов, силы прижатия, выполнения правил эксплуатации.
Методы и средства защиты от вибрации классифицируются в зависимости от степени контакта работающих с источником вибрации.
Борьбу с вибрацией можно эффективно проводить с помощью вибропоглощающих и виброизолирующих материалов и специальных устройств. В качестве средств индивидуальной защиты от вибрации используют специальную обувь на массивно резиновой подошве, рукавицы, перчатки, вкладыши, которые изготавливаются из упругодемпфирующих материалов. Важными моментами в системе мероприятий по снижению негативного воздействия шума и вибрации являются правильная организация труда и отдыха, постоянное медицинское наблюдение за состоянием здоровья операторов, специальные лечебно-профилактические мероприятия, такие, как гидромассаж, гидропроцедуры, витаминизация.
4.3 Мероприятия по улучшению экологических условий труда
В 2008 году на предприятии был проведен ряд природоохранных мероприятий, финансирование которых осуществлялось за счет собственных средств. Отчет о выполнении природоохранных мероприятий за 2008 год приведен в таблице 4.2.
Таблица 4.2 Отчет о выполнении природоохранных мероприятий за 2008 г.
Наименование мероприятий | Общая сметная стоимость, тыс. р. | Срок выполнения (год начала и окончания) | Освоено кап. вложений на 01.01.2009 г., тыс. р. | Примечание | |
% | В текущих ценах | ||||
1 | 2 | 3 | 4 | 5 | 6 |
Реконструкция очистных сооружений ливневой канализации | 2 197 070,00 | 2007-2009 | 42,9 | 942 225,00 | Коэффициент 1 220,657 |
Определение класса токсичности отходов | 10 000,00 | 2008 | 152,7 | 15 265,90 | --- |
Приобретение газо-пылеулавливающей установки «Улов-3000» | 7 466,20 | 2008 | 100,0 | 7 446,20 |
Производительность 3 тыс. м3/час |
Приобретение газо-пылеулавливающей установки «ПУ-1500» | 2 554,50 | 2008 | 100,0 | 2 554,50 |
Производительность 1,5 тыс. м3/час |
Установка для ультразвуковой сварки | 284 358,66 | 2008 | 100,0 | 284 358,66 | Снижение выбросов на 4, 2 тонн/год |
Затраты предприятия на охрану окружающей среды, экологические платежи и плата за природные ресурсы приведены в приложении Г.
За счет внедрения природоохранных мероприятий в 2008 году были снижены экологические налоги за выбросы и сбросы загрязняющих веществ на 30 223,2 тыс. р.
В 2008 году за нарушение природоохранного законодательства предприятием было выплачено 6 543,9 тыс. р. (добыча водных ресурсов сверх установленных лимитов).
За счет функционирования Системы управления окружающей средой на предприятии в 2008 году были снижены экологические налоги на 66 011,925 тыс. р.
В 2008 году Министерством промышленности Республики Беларусь проводилась проверка организации и осуществления производственного экологического контроля, локального мониторинга окружающей среды, соблюдения технологических регламентов и экологических нормативов на МЗХ.
Минским городским комитетом природных ресурсов и охраны окружающей среды проводилась проверка количественного и качественного состава выбросов загрязняющих веществ от стационарных источников в рамках локального мониторинга. Результаты проверки подтвердили соответствие количественного и качественного состава выбросов загрязняющих веществ проекту предельно допустимых выбросов МЗХ.
ЗАКЛЮЧЕНИЕ
Себестоимость продукции, работ, услуг представляет собой один из важнейших обобщающих показателей деятельности организации, отражающий эффективность использования всей совокупности ресурсов, результатов инновационной деятельности в области техники, технологии, организации труда, производства и управления. Являясь основой ценообразования и конкурентоспособности продукции, себестоимость постоянно повышается в силу следующих причин: повышения цен на материальные ресурсы; повышения заработной платы в связи с ростом минимальной базовой величины и тарифной ставки первого разряда; переоценки основных фондов и, в связи с этим, повышения амортизационных отчислений; переоценки оборотных средств в связи с инфляционными процессами и т.д.
Цель дипломного проекта: на основании информации о развитии предприятия в прошлом и данных о производственно-хозяйственной и сбытовой деятельности за последние три года произвести анализ и установить возможные направления снижения себестоимости продукции.
Цель дипломного проекта была достигнута за счет:
– совершенствования организационной структуры предприятия;
– совершенствования методологии учета затрат;
– совершенствования методологии управления затратами.
В научно-исследовательском разделе были установлены, факторы, влияющие на изменение себестоимости продукции, источники, факторы и резервы снижения себестоимости производимой продукции. Так же была проанализирована мировая практика учета и распределения затрат.
В аналитическом разделе проведен анализ организационной структуры и основных производственных показателей: объема и структуры продукции, себестоимости, прибыли, рентабельности, финансовых результатов деятельности предприятия. На основании анализа были сделаны следующие выводы:
– Организационная структура предприятия в целом является эффективной, однако она не отвечает задаче комплексного управления затратами производственно-хозяйственной деятельности предприятия и себестоимостью производимой продукции в частности.
– Объем производимой и реализуемой продукции характеризуется тенденцией к росту, однако затраты на рубль растут более высокими темпами, что свидетельствует о наличии резервов снижения затрат на производство и реализацию.
– В себестоимости продукции основную долю составляю сырье и материалы (около 70%), второе место по значимости занимает статья средства на оплату труда. Остальные статьи оказываю меньшее влияние на структуру себестоимости.
– Предприятие является прибыльным с достаточно высоким уровнем рентабельности. Однако в 2008 году наметилось существенное сокращение прибыли, что обусловлено значительным ростом цен на сырье.
В проектном разделе на основании выявленных недостатков были предложены следующие мероприятия, позволяющие повысить эффективность системы управления себестоимостью выпускаемой продукции, а также снизить затраты на выпуск продукции:
– предложение по организации отдела контроллинга;
– предложение по совершенствованию методологии управления затратами;
– предложение по совершенствованию методологии учета затрат;
– предложения по оптимизации экологических условий труда, в частности: приобретение газо-пылеулавливающих установок, установки для ультразвуковой сварки, снижение уровня шума и вибрации.
Как было установлено из анализа организационной структуры, функции управления затратами, и себестоимостью в частности, размыты. В целях систематизации работ по управлению себестоимостью производимой продукции был спроектирован отдел контроллинга. Спроектированная служба состоит из 5 сотрудников:
а) начальник службы контроллинга;
б) контроллер — куратор цехов (два сотрудника);
в) контроллер — специалист по управленческому учету;
г) контроллер — специалист по информационным системам.
Отдел контроллинга является координационным центром работы по управлению затратами предприятия. Планируется эффект в размере 3 028 345 тыс. р.
Очевидно, что отдел, специализирующийся на управлении затратами, должен иметь современный методологический аппарат для выполнения своих задач. В связи с этим в качестве основного инструмента управления затратами была использована система целевого планирования затрат.
Основу концепции составляет изменение взгляда на взаимозависимость цены, прибыли и себестоимости. Основным условием для расчетов являются цена, по которой можно осуществить продажи в планируемых объемах, и прибыль, уменьшение суммы которой лишает смысла работы над этим продуктом. Итогом расчетов является себестоимость, в которую необходимо вписаться при разработке, производстве и продвижении продукта. Использование системы целевого планирования затрат позволит изменить подход к управлению себестоимостью производимой продукции. Определяя себестоимость как производную от цены, являющейся в условиях рыночной экономики константой, система повышает мотивационный уровень работы по снижению уровня затрат на производство продукции. Экономический эффект от внедрения мероприятий в рамках целевого планирования затрат составит 756 813,427 тыс. р.
Для достижения цели снижения себестоимости необходимо иметь представление о реальном уровне затрат на производимую продукцию.
В результате рассмотрения основных методов учета и распределения затрат, наиболее отвечающим целям мониторинга уровня себестоимости и определения избыточных затрат, был признан пооперационный метод учета затрат.
Использование пооперационного метода учета затрат в производстве позволит с высокой точностью оценить себестоимость продукции, избежав искажений, характерных для традиционных систем учета затрат. Пооперационный метод позволяет принимать обоснованные решения в отношении:
– снижения издержек. Реальная картина издержек дает возможность точнее определять виды затрат, которые необходимо оптимизировать;
– ценовой политики. Точное отнесение издержек на объекты калькуляции позволяет определить нижнюю границу цен, дальнейшее снижение которых относительно такой границы ведет к убыточности продукта;
– товарно-ассортиментной политики. Реальная себестоимость позволяет разработать программу действий по отношению к тому или иному продукту - снять с производства, оптимизировать издержки или поддерживать на текущем уровне;
– оценки стоимости операций. Можно решить, целесообразно ли передавать те или иные операции подрядчикам или необходимо проводить организационные преобразования.
Использование пооперационного метода расчета себестоимости позволит оптимизировать ассортимент выпускаемой продукции за счет дифференцированного подхода к различным моделям продукции и оценить целесообразность производства отдельных комплектующих собственными силами.
Внедрение пооперационного метода потребует значительных единовременных капитальных вложений. За первый год затраты превысят результат на 61 845, 960 тыс.р. Планируемый срок окупаемости проекта – 3,4 года.
Итого суммарный экономический эффект от внедрения мероприятий составил: 3 723 313 тыс. р.
СПИСОК ЛИТЕРАТУРЫ
1 Анализ хозяйственной деятельности в промышленности : учебник / Л.А. Богдановская [и др.] ; под общ. ред. В.И. Стражева. – Минск : Выш. шк., 1996.
2 Вумек, Дж.П. Бережливое производство. Как избавиться от потерь и добиться процветания вашей компании / Дж. П. Вумек, Т. Даниел Джонс - М. : Альпина Бизнес Букс, 2008.
3 Грибоедова И А. Статистика в промышленности [Текст] : учеб.-метод. комплекс / И.А. Грибоедова, Д.Ю. Бусыгин ; под ред. И.А. Грибоедовой. – Минск : Изд-во МИУ, 2006.
4 Конструкторская документация. Чертежи деталей : учеб. пособие по курсу «Конструирование РЭУ» для студ. спец. «Проектирование и производство РЭС» / Ж.С. Воробьева [и др.]. – Минск : БГУИР, 2003.
5 Основные положения по составу затрат, включаемых в себестоимость продукции (работ, услуг) от 20/01/2009.
6 Охрана труда : учеб. пособие для учащихся учреждений, обеспечивающих получение проф. технического образования / И.Ю. Крыжановский [и др.]. – Минск: Беларусь, 2007.
7 Положение об отделе планирования и экономического анализа // К приказу по заводу, 2005.
8 Пояснительная записка МЗХ ЗАО «Атлант» к годовому отчету / 2006.
9 Пояснительная записка МЗХ ЗАО «Атлант» к годовому отчету / 2007.
10 Пояснительная записка МЗХ ЗАО «Атлант» к годовому отчету / 2008.
11 Пурыгин А.В. Определение себестоимости методом Activity based costing / А.В. Пурыгин // Планово-экономический отдел. – 2008. - №5(5). - С. 30-39.
12 Савицкая Г.В. Анализ хозяйственной деятельности предприятия : 4-е изд., перераб. и доп. / Г.В. Савицкая. – Минск : Новое знание, 2000.
13 Сборник методик по расчету выбросов в атмосферу загрязняющих веществ различными производствами. – Л. : Гидрометеоиздат, 1986.
14 Светов А.Ф. Уметь нужно платить меньше, а получать больше. Резервы снижения себестоимости продукции / А.Ф. Светов // ЭФУ. – 2008. - №3(3). - С.40-43.
15 Смольский А.П. Калькулирование себестоимости по переменным расходам как инструмент управления / А.П. Смольский // Планово-экономический отдел. – 2008. - №7(7). - С. 28-35.
16 Старова Л.И. Методические указания к практическим занятиям по курсам «Технико-экономический анализ производственно-хозяйственной деятельности предприятия» и «Анализ хозяйственной деятельности предприятия» / Л.И. Старова. – Минск: БГУИР, 2001.
17 Суворов Г.А. Гигиеническое нормирование производственных шумов и вибраций / Г.А. Суворов [и др.]. - М. : Медицина, 1984.
18 Суша Г.З. Экономика предприятия : учеб. пособие / Г.З. Суша. - М.: Новое знание, 2003.
19 Хрипач В.Я. Экономика предприятия : учеб. пособие / В.Я. Хрипач. - М. : Финансы, учет, аудит, 1997.
20 Челноков, А.А. Охрана труда: учеб. пособие / А.А. Челноков, Л.Ф. Ющенко. – Минск: Выш. шк., 2006.
21 Шимова, О.С. Основы экологии и экономика природопользования / О.С. Шимова, Н.К. Соколовский. – Минск: БГЭУ, 2002.
22 Экономика и организация производства: руководство по преддипломной практике и дипломному проектированию для студ. всех форм обуч. / Э.А. Афитов [и др.]; под ред. В.П. Пашуто. – Минск : БГУИР, 2007.
23 Экономика предприятия: учеб. пособие / Л.Н. Нехорошева [и др.]; под общ.ред. Л.Н. Нехорошевой. – 3-е изд. – Минск : Выш. шк., 2005.
ПРИЛОЖЕНИЕ А
(обязательное)
Организационная структура МЗХ ЗАО «Атлант»
ПРИЛОЖЕНИЕ Б
(обязательное)
Характеристика очистных сооружений Минского завода холодильников
Наименование очистного сооружения и метод очистки |
Пропускная способность, м3/год |
Эффективность очистки | |||||
Проектная | Фактическая | Наименование ингредиента | Средняя концентрация по проекту | Средняя концентрация фактически | |||
Поступило, мг/л | Сброшено, мг/л | Поступило, мг/л | Сброшено, мг/л ПДС | ||||
1 | 2 | 3 | 4 | 5 | 6 | 7 | 8 |
Очистные сооружения гальваники Метод очистки: гальванокоагуляция, нейтрализация реагентная, отстаивание, фильтрация |
120 000 | 70 000 |
рН; алюминий; железо; медь; никель; цинк; хром (общ.) |
2,00 36,00 21,00 22,00 32,00 46,00 17,00 |
6,5-8,5 0,5 2,0 0,15 0,15 -- 0,04 |
1,93 4,70 30,60 1,40 1,00 12,00 17,50 |
6,5-8,5 1,0 4,0 1,0 1,0 4,0 1,6 |
Очистные сооружения окраски (корпус №1) Метод очистки: нейтрализация реагентная, отстаивание, фильтрация |
154 000 | 154 000 |
рН; железо; медь; никель; цинк; хром (общ.) |
9,80 -- -- -- -- 0,04 |
6,5-8,500 2,00 0,015 0,15 -- 0,04 |
12,37 1,90 1,00 1,00 3,10 4,80 |
6,5-8,5 4,0 1,0 1,0 4,0 1,6 |
Очистные сооружения окраски (корпус №12) Метод очистки: нейтрализация реагентная, отстаивание, фильтрация |
10 000 | 6 000 |
рН; взвешенные вещества; железо; медь; никель; цинк; хром (общ.) |
10,0 600,0 4,0 1,4 1,4 2,8 -- |
6,0-9,0 300 2,0 1,0 1,0 2,0 0,5 |
10,0 600 4,0 1,4 1,4 2,8 -- |
6,0-9,0 300,0 2,0 1,0 1,0 1,0 --- |
Очистные сооружения мойки автотранспорта Методы очистки: отстаивание, фильтрация |
10 000 | 7 000 |
взвешенные вещества; нефтепродукты |
3 000,0 100,0 |
18,0 4,0 |
3 000,0 100,0 |
18,0 4,0 |
Очистные сооружения оборотной системы водоснабжения участка экструзии Методы очистки: флотация, фильтрация |
84 000 | 84 000 | взвешенные вещества | 300,0 | 5,0 | 300,0 | 5,0 |
Очистные сооружения промдождевых вод Методы очистки: флотация, отстаивание, фильтрация, хемосорбция |
200 000 | 200 000 |
взвешенные вещества; нефтепродукты; железо; БПК |
600,0 40,0 0,7 30,0 |
30,0 0,3 0,3 6,0 |
600,0 40,0 0,7 30,0 |
30,0 0,3 0,3 6,0 |
ПРИЛОЖЕНИЕ В
(обязательное)
Справка о затратах на охрану окружающей среды, экологические платежи и плата за природные ресурсы
Направление затрат | Затраты, тыс. руб. | |||
2005 | 2006 | 2007 | 2008 | |
1 | 2 | 3 | 4 | 5 |
1 Текущие затраты, всего | 1 129 966.4 | 2 148 145.0 | 1 699 396,5 | 2 050 063,3 |
1.1 Охрана и рациональное использование водных ресурсов | 396 901.5 | 1 382 673.2 | 673 279,7 | 995 613,7 |
в том числе выплачено другим предприятиям за прием и очистку сточных вод | 160 333.7 | 190 623.1 | 272 767,1 | 448 108,0 |
1.2 Охрана атмосферного воздуха | 335 211.2 | 387 988.4 | 417 996,7 | 398 053,0 |
1.3 Охрана окружающей среды от загрязнения отходами производства | 395 125.9 | 374 873.0 | 589 072,1 | 652 036,2 |
в том числе выплачено другим предприятиям за прием, хранение и обезвреживание отходов | 119 181.1 | 48 189.8 | 300 441,9 | 110 100,8 |
1.4 Экологическая паспортизация, сертификация, аудит и страхование | 2 727.8 | 2 610.4 | 19 048,0 | 4 360,4 |
2 Затраты на капитальный ремонт основных производственных фондов по ООС, всего | 125 302.4 | 606 736.9 | 193 711,5 | 72 827,6 |
3 Экологические налоги, всего | 155183.8 | 306 123.6 | 424 927,3 | 789 761,2 |
в том числе | ||||
3.1 За выбросы вредных веществ в атмосферный воздух от стационарных источников | 104 754.7 | 177 627.7 | 241 832,2 | 239 086,6 |
3.2 За выбросы вредных веществ в атмосферный воздух от передвижных источников | 32 609.5 | 63 071.0 | 85 846,1 | 111 676,9 |
3.3 За размещение отходов производства | 17 819.6 | 65 424.9 | 97 249,0 | 429 326,4 |
3.4 За сбросы загрязняющих веществ в водные объекты | 9 671,2 | |||
4 Плата за природные ресурсы | --- | --- | 97,3 | 6 704,1 |
в том числе | ||||
за добычу водных ресурсов (артезианская вода) | --- | --- | 97,3 | 6 704,1 |
5 Плата за землю | 525 148.5 | 864 963.4 | 1 112 625,9 | 1 644 697,0 |
6 Стоимость основных производственных фондов по ООС, всего | 3 613 506.0 | 4 849 350.9 | 9 594 857,2 | 7 226 603,5 |
в том числе | ||||
6.1 По охране рациональному использованию водных ресурсов | 2 098 123.0 | 3 011 772.7 | 9 594 857,2 | 4 840 534,4 |
6.2 По охране атмосферного воздуха | 583 916.0 | 808 258.5 | --- | 215 603,1 |
6.3 По использованию и обезвреживанию отходов | 931 467.0 | 1 029 319.7 | --- | 2 170 466,0 |