Реферат: Зубопротезное литье
Изготовление литых зубных протезов началось уже давно. Известно, например, что в 1820 г. филадельфийский зубной врач Гудсон отливал протезные пластинки из олова. Известны также так называемые хеопластические протезы — из олова, серебра, висмута и сурьмы.
Широкое распространение литые протезы получили значительно позже, когда был найден способ плавки золота и введения его в расплавленном виде в литейную форму посредством специальных приспособлений с применением давления пара, газа или центробежной силы.
Технология отливки складывается из следующих операций:
1) изготовление по гипсовой модели восковой формы,
2) погружение этой формы в покровную (формовочную) массу в цилиндре для получения литейной формы,
3) выжигание восковой модели,
4) плавка золота,
5) заливка золота в литейную форму.
Такая технология еще сохранилась во многих местах до настоящего времени. Остановимся на отдельных операциях технологии несколько подробнее. Необходимый протез изготавливают первоначально из воска, при этом весьма тщательно обрабатывают его вручную, применяя очень тонкий инструмент (шпатели и др.). Если восковая модель оказывается во всех отношениях безукоризненной, ее закрепляют на штифте на подставке (рис. 1).
После этого приступают к погружению восковой формы в
«паковочную» массу. Для этого подбирают цилиндр, называемый также кюветой
(опока), такого размера, чтобы в нем поместилась восковая модель. Паковочная
масса должна иметь высокую огнеупорность и достаточную прочность. Нагретая до
белого каления масса не должна давать трещин, не должна плавиться и давать
усадку. Кроме того, она должна быть достаточно пористой, чтобы
пропускать пары воздуха и газы от сгорания воска (табл. 1).
Рис.1. Восковая
модель на подставке.
Таблица 1
Состав паковочных масс
Состав |
Наименование элементов |
Количество частей |
1 |
Гипс ...............…………………….. Асбест ...............…………………... Кремнезем в порошке .......……….. |
2 1 1 |
2 |
Кремнезем .............……………….. Гипс ...............……………………... |
3 1 |
3 |
Каолин ..............…………………... Кварцевая мука ..........……………. |
1 1 |
4 |
Гипс ...............……………………... Смола в порошке…………………. Мрамор в порошке .........………… |
2 1 1 |
Паковочная масса замешивается с водой до сметанообразной консистенции.
Восковую модель сначала покрывают с помощью кисточки тонким слоем паковочной массы и после ее затвердевания надевают цилиндр (кювету) на модель, и заполняют паковочной массой.
После полного затвердевания цилиндр поворачивают вверх подставкой, которая легко вынимается. После легкого подогрева вынимают и штифт, на котором была посажена модель на подставку. Оставшееся отверстие будет служить литниковым ходом. Теперь остается выжечь восковую модель протеза, чтобы получить литейную форму. Для этого цилиндр помещают в печь и сначала в слабом пламени горелки медленно просушивают массу, а затем повышают температуру до полного выжигания воска. В таком виде литейная форма становится готовой для заливки.
Заливка золота производится с
помощью различных приспособлений, называемых у зубных техников литейными
аппаратами, для обеспечения прогона жидкого металла давлением пара через
тонкий литник. Цилиндр, или кювету, с литейной готовой формой устанавливают на
треножник (рис 2.) и когда золото расплавится с помощью горелки, цилиндр
накрывают штемпелем — крышкой, обмазанной мольдином (глина с глицерином). От
соприкосновения мольдина с разогретым цилиндром образующиеся пары глицерина
создают давление, под действием которого жидкое золото вгоняется в форму.
|
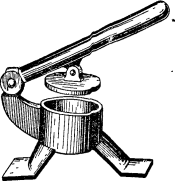
Помимо описанного способа заливки, применяются и другие. При литье деталей зубопротезных конструкций количества металла обычно недостаточно для того, чтобы он силой своей тяжести заполнил литейную форму. Для этой цели применяют аппараты, дейсгвие которых основано на разности давления, т.е. создают повышенное давление над расплавленным металлом или отрицательное давление (вакуум) внутри формы. На рис.3. показан аппарат с давлением от баллона сжатого воздуха, а на рис.4. — другой аппарат, действие которого основано на следующем. Заполняют асбестом
Рис.3. Литейный аппарат Рис.4. Прибор для литья под
с использованием давления давлением водяных паров.
сжатого воздуха.
или мольдином металлическую крышку, прикрепленную к ручке аппарата, а кювету устанавливают на подставке под крышкой: когда металл расплавится, ручкой надавливают на крышку, которая закрывает всю поверхность кюветы. Повышение давления создается при испарении влажного асбеста или мольдина.
Для этой же цели применяют аппараты, действующие по принципу центробежной силы. Несмотря на то, что существует много центробежных аппаратов, работающих при помощи электричества, наиболее широкое распространение получила ручная центрифуга, имеющая весьма простое устройство. В деревянной ручке укрепляют неподвижно винт, на который надевают при помощи подвижного крючка железную проволоку толщиной 3-4 мм и длиной 15-20 см. На конце проволоки имеется петля, соединяющаяся подвижно с дугой, на концах которой находится металлическая чашка для установки кюветы во время отливки. Кювету нагревают и вставляют в эту чашку, а в воронку кюветы помещают золото. При помощи паяльного аппарата направляют струю пламени на золото до его расплавления. Затем центрифугу приводят в движение, и после 3-4 поворотов металл вгоняется в кювету.
Во время расплавления золота к нему во избежание окисления добавляют порошок буры.
В последнее время для заполнения кюветы формовочной массой применяется вибрация литейной формы.
Вместо золота в зубопротезном деле начали широко применять нержавеющую сталь марок Х18Н9 и ЭИ95. Протезы из стали отливают по методу выплавляемых моделей.
Для литья деталей зубопротезных конструкций необходимо произвести следующие операции:
1) вклеивание литников из металлической проволоки диаметром 2-2,5 мм и длиной 3-3,5 см в нерабочую часть восковых моделей;
2) соединение восковых моделей в общий блок и приклеивание его литниками к деревянному конусу, покрытому воском;
3) покрытие восковых моделей огнеупорной оболочкой;
4) покрытие металлической опокой-кюветой деревянного конуса с восковыми моделями;
5) заливка формовочной массой на моторе-вибраторе опоки с восковыми моделями;
6) удаление литников из опоки и выплавление восковых моделей в муфельной печи;
7) обжиг формы в опоке;
8) расплавления стали и заливка ею формы;
9) удаление отлитых деталей из опоки и очистка их от формовочной массы;
10) отделение литников от деталей и окончательная очистка их от огнеупорной массы с помощью металлической щетки на шлифовальном круге.
В крупных лабораториях восковые модели делают в большом количестве и их комбинируют «в елку».
Формовочной массой для литья стали служит состав из 90% корунда (минутник №10) и 10% гипса.
Для покрытия восковых моделей огнеупорной оболочкой перед их формовкой в кюветах приготовляют раствор, состоящий из 2% целлулоида (рентгеновская пленка или кинопленка) и 98% ацетона. К этому раствору добавляют минутник №30 до состояния жидкой кашицы. Если нет тонкого минутник, можно применять тонкий кварц.
Может быть также использована смесь из одной части гидролизованного этилсиликата и двух частей маршалита.
С 1951 г. стали применять смесь из 90% кристаллического кварцита и 9% окиси кальция. Смесь замешивают на 1-процентном водном растворе жидкого стекла.
Выплавление восковых моделей проводят в муфельных печах при температуре 600-800 градусов в течение полутора-двух часов.
Аппарат для расплавления и литья стали состоит из двух основных частей – электрической печи и вакуум-насоса (рис.5).
Электропечь представляет собой металлический каркас 1
с находящимся внутри огнеупорным керамическим цилиндром 3. Каркас имеет
съемную крышку. Между каркасом и керамическим цилиндром находится асбест 2.
Внутри керамического цилиндра имеется углубление 4, в которое вставлены
электроды 5 и тигель для расплавления стали 6, изготовляемой из
электрокорунда кварцита и других огнеупорных материалов. Тигель может быть
также изготовлен из кварцевой трубки соответствующего диаметра и толщины.
Промежуток между тиглем и керамической футеровкой заполнен криптолом — мелкими кусочками графитизированного или угольного электродного боя величиной 5—6 мм. При включении тока между кусочками графита возникают вольтовы микродуги и выделяется значительное количество тепла, что ведет к нагреву огнеупорного тигля, в котором находится сталь; последняя начинает плавиться. Углубление в цилиндре закрыто керамической крышкой 7 с отверстием в центре. Электропечь укреплена на двух стойких 8, на оси которых с правой стороны находится рукоятка 9 для поворота печи при заливке стали в опоку.
Когда сталь в тигле расплавлена, на керамическую
Рис.5. Схема устройства крышку устанавливают кювету 12, которую плотно при-
для плавки стали жимают подвижной дугой 10 цилиндрического фланца 11.
системы Д. Н. Цитрина Фланец имеет трубку, соединенную с вакуум-насосом с
помощью резинового шланга, через который отсасываются газы и создается отрицательное давление в опоке.
Вакуум-насосы могут быть водоструйными и механическими. Водоструйный насос состоит из двух резиновых шлангов 13, стеклянной бутыли и вакуумметра.
В комплект электропечи входят: понижающий трансформатор на 30, 45, 60, 75, 90 в и 40, 50 а, реостат, вольтметр, амперметр и термопара с гальванометром.
Питание электропечи осуществляется от электросети.
Отливка центробежным способом производится
специальной печью (рис.6). Металлический корпус электропечи для центробежного
литья изготовлен из листовой стали толщиной 2,5 см; толщина дна — 5 мм.
Внутри корпуса на асбестовой засыпке помещается высокоогнеупорная хромомагнезитовая
футеровка, изготовленная из двух половинок, соединяющихся в вертикальной
плоскости, проходящей через ось печи.
Кольцевое пространство между футеровкой и обечайкой корпуса заполнено асбестовой засыпкой.
В цилиндрическом рабочем пространстве печи, образуемом половинками футеровки, находятся два угольных электрода и тигель для расплавления металла, изготовленный из высокоогнеупорного материала. Остальной объем рабочего пространства заполнен мелкими кусочками гра-
фита.
Рис.6. Электропечь для Сверху полость печи закрыта хромомагнезитовой крышкой,
плавки стали системы на которой установлен массивный стальной фланец; в верх- И. П. Корнеева. нюю расточку фланца вставляется цилиндрическая сталь-
ная опока, в которой находятся заформованные восковые модели для отливки.
Сверху печь закрывается стальной крышкой, которая ставится на слой обмазки и плотно прижимается к обечайке корпуса двумя замками накидного типа.
Для сохранения вертикального положения печи, с целью предохранения ее от опрокидывания, к днищу корпуса прикреплен чугунный противовес. В полость противовеса выходят нижние концы угольных электродов, от которых идут провода, защищенные изоляционными бусами.
В нижней части корпуса печи расположены две полуоси. Для точного установления полуосей на одном диаметре фланцы их центрируются штифтами, закрепленными в обечайке корпуса. Шейки полуосей опираются на шарикоподшипники, находящиеся в расточках двух литых чугунных стоек.
На правую удлиненную полуось насажено на шпонке малое зубчатое колесо; оно сцепляется с большим зубчатым колесом (передаточное отношение 3:5), вращающимся с помощью рукоятки. К полуосям прикреплены вертикальные планки, соединенные наверху стяжкой. В отверстии стяжки, расположенном на оси печи, может перемещаться вертикальный стержень, к нижнему концу которого прикреплена крышка опоки.
Внутри подставки, внизу, помещен трансформатор, установленный на дощатом настиле и прикрепленный болтами к каркасу подставки. Нижняя часть каркаса подставки закрыта с трех сторон проволочной сеткой, а с одной стороны — съемным стальным листом. В верхней части подставки, справа к ней, прикреплен наклонно расположенный кожух, в котором помещен переключатель.
Электрощит с измерительными приборами прикрепляют к стене.
Для изготовления тиглей из огнеупорной массы имеется специальный разборный металлический штамп, состоящий из двух половинок, стягиваемых на обоих концах гайками с накаткой. В огнеупорную массу для изготовления тиглей входит: 30% корунда № 325, 30% электрокорунда № 100, 40% шамотной глины. Указанный материал замешивают на жидкости, состоящей из 90% воды и 10% отработанного машинного масла. Полученную смесь закладывают в штамп и прессуют. Затем тигель осторожно извлекают из пресс-формы и ставят в муфельную печь для просушки на l,5-2 часа при температуре 300-400°.
Окончательную прокалку тигля производят в литейной печи перед плавкой в течение 15—20 мин. при температуре 1200—1400°.
В центре рабочего пространства печи помещают тигель, в который закладывают 1—2 кубика нержавеющей стали, в зависимости от количества деталей, подлежащих отливке. Остальное пространство, как уже указывалось, заполняют кусочками графита и закрывают сверху конусной хромомагнезитовой крышкой. На крышку в центре ставят верхний стальной фланец; остальную верхнюю часть печи покрывают слоем обмазки, а крышку печи соединяют замками с кромкой корпуса. Отверстие фланца обмазывают слоем огнеупорной массы, толщина которого зависит от диаметра тигля.
1-термитная смесь;
2-шамотно-магнезитовый тигель;
3-стальной кожух,
4-магнезитовый стакан;
5- сменный штепсель;
6- запорный гвоздь.
Рис.7. Вращение печи для Рис.8. Тигель для сжигания
заливки литейной формы термита
После выплавки восковых моделей в расточку фланца устанавливают опоку- кювету. Через 30—40 мин , когда опока остынет, ее накрывают крышкой и весь узел закрепляют защитной рукояткой. Затем включают электрический ток. Рабочее напряжение регулируют с помощью специального реостата в соответствии с заданным режимом плавки.
После расплавления металла в тигле ток выключают, размыкают штепсельные соединения и резким движением начинают вращать рукоятку, развивая необходимую окружную скорость (рис.7), при этом расплавленный металл заполняет полость формы и под действием центробежной силы уплотняется в ней.
Кроме указанных литейных аппаратов, для отливки деталей зубопротезных конструкций применяют ацетилено-кислородные установки, а также производят отливку с помощью вольтовой дуги. Эти два способа отливки деталей из нержавеющей стали, особенно с помощью вольтовой дуги, имеют существенный недостаток: сталь во время расплавления слишком сильно насыщается углеродом вследствие чего теряет необходимые физические и химические свойства по стойкости против коррозии.
Существует также способ литья деталей зубопротезных конструкций из нержавеющей стали с помощью термитной смеси независимо от наличия источника электроэнергии.
Термит представляет собой смесь порошка алюминия и специально обработанной железной окалины. Алюминий благодаря большому сродству с кислородом способен восстанавливать окислы металлов с выделением при этой реакции большого количества тепла.
Реакция тепла протекает всего в течение 10—15 сек., при этом продукты реакции расплавляются и перегреваются до температуры 2600— 2700°. Реакция железо-алюминиевого термита идет по формуле:
3FeO х Fe Оз + 8Al -> 4А1гОз + 9 Fe + 793,5 кал.
Для возбуждения термитной реакции необходимо сообщить термитной смеси температуру не ниже 1250°; для этой цели применяют специальные зажигательные средства.
Сжигание термита производят в специальных тиглях, футерованных магнезитом (рис.8).
После окончания термитной реакции благодаря значительной разнице в удельных весах шлак (Al O ) концентрируется наверху, а металл опускается на дно тигля.
Чтобы получить нержавеющую сталь в качестве конечного продукта термитной реакции, в состав термитной смеси вводят в гранулированном виде необходимое количество компонентов, входящих в состав нержавеющей стали. Полученная таким образом термитная нержавеющая сталь характеризуется значительной жидкотекучестью, что обеспечивает получение высококачественного литья деталей зубопротезных конструкций.
Разработка модели технологического процесса получения ребристых труб и ... | |
СОДЕРЖАНИЕ ВВЕДЕНИЕ 4 ЛИТЕРАТУРА 116 ВВЕДЕНИЕ Рациональное использование природных ресурсов и энергии является важнейшей задачей производства ... Прежде чем приступить к проектированию технологии изготовления отливки, необходимо оценить возможности и целесообразность выполнения заказа на данном предприятии, руководствуясь ... Сравним плоскую отливку (плиту) с простейшим полым бесконечным цилиндром (Рис.5-2), т.к. в нашем случае основной элемент конструкции отливки теплообменник - труба, т.е. полый ... |
Раздел: Рефераты по технологии Тип: реферат |
Литье | |
ХАРАКТЕРИСТИКА ЛИТЕЙНОГО ПРОИЗВОДСТВА К Изготовление моделей, стержневых ящиков и другой оснастки раткая характеристика процесса получения отливок и ... Литьем получают разнообразные конструкции отливок массой от нескольких граммов до 300 т, длиной от нескольких сантиметров до 20 м, со стенками толщиной 0,5-500 мм (блоки цилиндров ... 2, г) в литейных опоках 5, 5. Литейная опока - приспособление для удержания формовочной смеси при изготовлении формы. Перед плавкой в электроде-держателе 2 печи устанавливают электрод 9, а перед сливным носком тигля 4 укрепляют литейную форму 7, После этого кожух 5 печи герметизируют и вакуумируют ... |
Раздел: Рефераты по технологии Тип: реферат |
Производство отливок из сплавов цветных металлов | |
Содержание: Введение 2 Общие сведения о производстве отливок из сплавов цветных металлов: Общая характеристика и классификация отливок Требования к ... Основными способами получения отливок из бронзы и сплавов серебра и золота были литье ij каменные формы и литье по воску. Плавильно-литейные комплексы, состоящие из плавильной печи - миксера - литейной машины, используют при литье слитков из алюминиевых, магниевых и медных сплавов непрерывным методом. |
Раздел: Рефераты по технологии Тип: реферат |
Проект литейного цеха стального литья автозавода мощностью 30000 тонн | |
Министерство образования и науки Украины Кафедра ТОЛП "Проектирование литейных цехов" Тема: "Проект литейного цеха стального литья автозавода ... Точная программа предусматривает разработку технологических данных для каждой отливки и применяется при проектировании литейных цехов крупносерийного и массового производства с ... Литейные цехи обладают большим количеством дорогостоящей оснастки (модели, стержневые ящики, опоки и др.), хранение которой организуется в специально оборудованных складах.. |
Раздел: Промышленность, производство Тип: курсовая работа |
Алюминий и его сплавы. Особенности получения отливок | |
Реферат выполнил студент 2-го курса факультета автомобилестроения, группа: 4ЗАА5 Кабанов А. М. Московский Государственный Технический Университет МАМИ ... При литье в кокиль наряду с дефектами, обусловленными высокими скоростями движения расплава в полости литейной формы и несоблюдением требований направленного затвердевания (газовая ... Заполнение форм металлом осуществляют давлением сжатого осушенного воздуха (18-80 кПа), подаваемого на поверхность расплава в тигле, нагретого до 720-750 °С. Под действием этого ... |
Раздел: Промышленность, производство Тип: реферат |